Introduction: In recent years, wind power has been developed around the world in order to provide a more sustainable alternative to electricity production. In the United States, for example, total annual electricity production from wind power has increased from 6 billion kilowatt hours in 2000 to approximately 380 billion kilowatt hours in 2021. According to the US Energy Information Administration (EIA), this represents approximately 9.2% of total utility-scale electricity generation in the US. There are still many challenges to overcome ahead, but progress is worth acknowledging. Amongst these challenges, some customers feel that wind turbines cannot be built unconditionally, while also considering the recyclability of the blades produced.
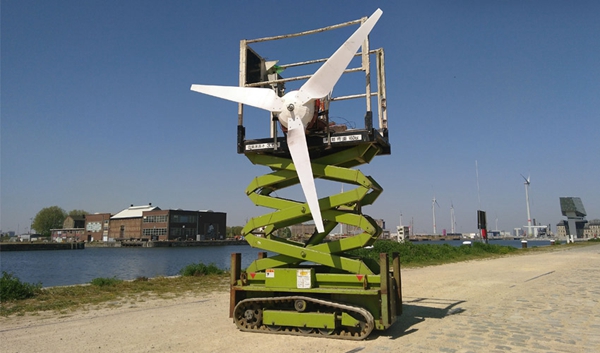
The From Waste to Wind association in Belgium is said to have been set up to address these challenges. It uses additive manufacturing techniques, mainly fused deposition modelling (FDM), to design wind turbines from recycled plastic. Bram, the founder of the non-profit organisation From Waste to Wind, had earlier gained valuable experience in conducting research on the environmental impact of large wind turbines in the Flemish government sector. From Waste to Wind has already received an international award and additional support from the Antwerp Climate Fund in Belgium.
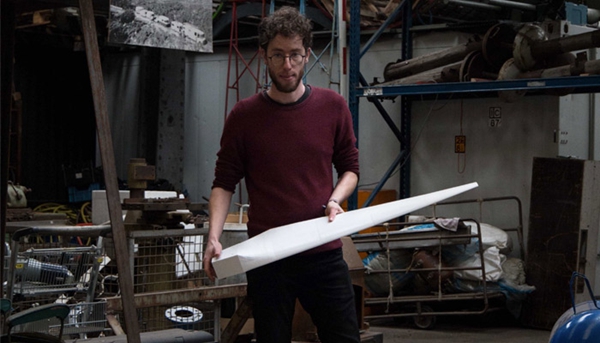
△BramPeirs holding a 3D printed wind turbine blade
Background to the creation of From Waste to Wind
While working for the Flemish government, Bram noticed that there was still a lot of resistance to the promotion of wind turbines. Although there were already fairly strict rules in place to limit the environmental impact of wind turbines, people were not aware of these rules. They feared that wind turbines would cause noise pollution and block their view, so they didn't want them in their gardens. To get people to look at wind power differently, Bram started experimenting with making wind turbines out of old barrels, using magnets from old hard drives and meeting like-minded people on the internet.
Bram now works with Time Circus, a charity group that makes all sorts of things from recycled materials, and they also run Loods 21 and Bar Paniek in Belgium. timeCircus' original homemade wind turbine blades were made from PVC sewer pipe, which was not very UV resistant, and the blades had broken, causing power failures. Bram eventually bought a printer for €200 and repaired the blades using 3D printing.
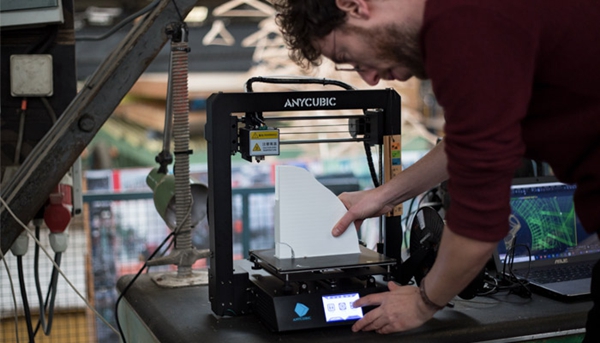
Photo credit: From Waste to Wind
Printing plastic is sometimes not as easy as it looks, it can shrink and warp, and it took Bram several months to get it right. Bram later printed a completely customised wind turbine measuring 20x20x20 cm. This wind turbine worked well for several months and it won Bram a $10,000 prize at Hackaday (an international platform for innovative creators), which was a great encouragement for them.
In order to break down barriers to renewable energy, especially small-scale wind energy, and bring energy production closer to people, Bram created the From Waste to Wind association. The company's current business model focuses on doing research and raising awareness, which they do with prizes and subsidies. In addition, they have received a grant from the City of Antwerp Climate Fund, which is a great boost to the company's philanthropic goals.
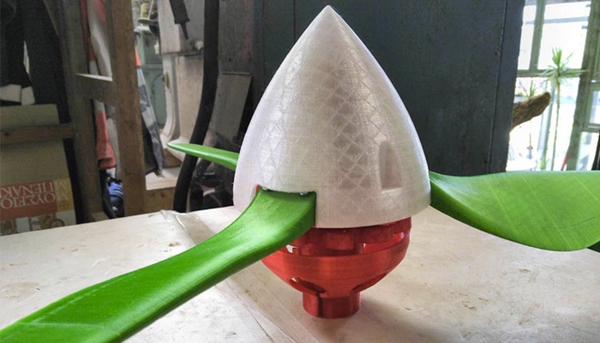
△Prototype wind turbine made of rPET. Photo credit: From Waste to Wind
3D printing for sustainability
Recycling the blades of wind turbines has always been a big problem, as the fibres and resin cannot be separated when they reach the end of their useful life after 20 years. The only thing that can be done is to grind them up and put them in a landfill or reuse them in asphalt. In the USA they are often buried in landfills.
Pure plastic blades can be fully recycled, unlike the glass fibre reinforced blades used by other manufacturers. bram has deliberately chosen to print reinforced plastics without added fibres. This is because with today's recycling methods, plastics are still "contaminated" and have much less potential for reuse. Today, much of the plastic waste is generated during the printing process, and then there is the uncertainty about the origin of the material. For example, PLA biomaterial may be produced somewhere and then shipped to another industrial facility, where it is processed into filament. This is why Bram chose to use rPET, which is made from recycled PET, the same plastic used for plastic bottles. It has to be recycled anyway and is already available locally, and it also has better mechanical properties than PLA.
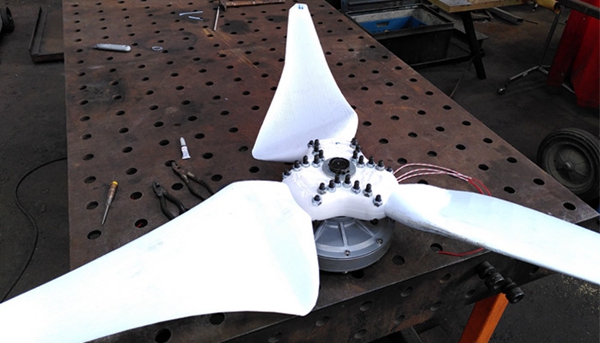
△Photo credit: From Waste to Wind
From Waste to Wind's future projects
From Waste to Wind plan to build larger wind turbines, up to 4 metres long, which will generate 50% of the energy needed for an average household, complementing photovoltaic power. They also plan to connect all the wind turbines to a computer so that the consumer can always see how much energy his wind turbine produces and also safety parameters such as vibrations. From Waste to Wind is currently developing their own MPPT controller, which will be completely open source.
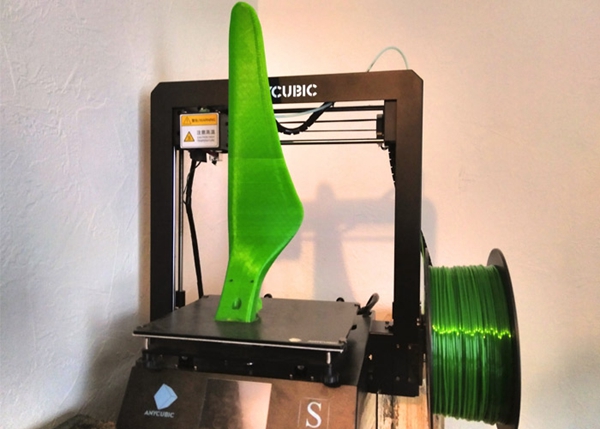
△Photo credit: From Waste to Wind