Italian researchers have designed and fabricated an artificial pneumatic muscle composed of 3D-printed structures that can stretch and contract as needed. It is a pneumatic hand made in a single printing process and composed of 18 different GRACE (actuators capable of contracting and elongating), reports the journal Science-Robotics.
The creation of artificial muscles is one of the goals pursued in the field of robotics, because in nature, muscle tissue has complex characteristics, from fast and powerful contractions to small and precise changes in shape that can be flexibly controlled, and also allows highly flexible movements. Individual muscle fibers can only achieve contraction, nevertheless, but it is their specific arrangement in a complex musculature that enables joint deformations such as bending, twisting and countermovement.
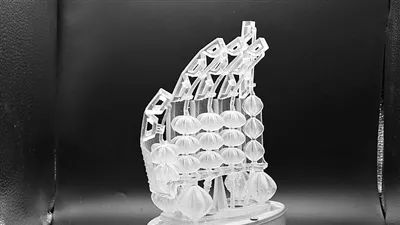
△ Italian researchers demonstrate the versatility of the actuator, a pneumatic hand composed of 18 different GRACEs, manufactured using a single printing process. Image credit: Italian Institute of Technology
The research team tried to make a breakthrough this time starting with a single pneumatic actuator. Each actuator can be simply expanded, extended and contracted by its geometry, similar to a spindle with pleats, including a separate unit that can be 3D printed and fabricated using different materials and different sizes. The various GRACEs are printed and assembled into complex architectures to provide the desired type of motion.
The GRACEs can be made in different sizes, which can vary their performance in terms of deformation and strength, and they can also be manufactured with a variety of materials and techniques and even built into the structure to be fabricated, according to the researchers.
The researchers used a commercial 3D printer to create pneumatic hands in a single printing process and demonstrated the properties of GRACE. The material used to print the pneumatic hand is a soft resin that contains 18 GRACEs of different sizes and shapes, so that only a few tenths of a Pa of pressure is needed to bend the fingers, twist the palm and rotate the wrist. The pneumatic hand weighs about 100 grams and is comparable in size to a human hand.
The new design allows pneumatic hands to support more than 1,000 times their own weight, depending on the materials used to make them. In fact, the force generated and the pressure required can be increased or decreased by using materials with different stiffnesses and modifying the thickness of the membranes that make up these actuators, while maintaining the same contraction and extension properties.