Recently, OECHSLER from Germany has developed a hiking backpack that uses 3D printed shock absorbing mesh material for the first time, an innovation that aims to take the field of additive manufacturing to a new level, according to Mohou.com. oechsler's proposal won the red dot design concept award, which is given annually to the best product design. oechsler says that with this backpack hikers will have a more comfortable backpacking experience when hiking.
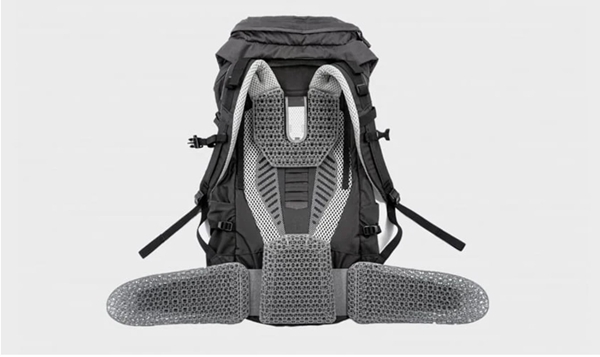
OECHSLER's hiking backpack
As we have seen in many other contexts, the use of 3D printing in consumer products, especially sporting goods, offers many great benefits to businesses. Many everyday products can already be manufactured with additive manufacturing, such as the soles of Adidas 4DFWD sneakers, the Squishy Mouse computer mouse or the VAEN bicycle saddle for example, but what is most interesting is that all of these items, as well as the OECHSLER backpack, have something in common. 3D printing technology makes it possible to create complexity in shapes, providing a great opportunity to create impact absorbing and provide the user with the possibility of a mesh structure that offers greater comfort.
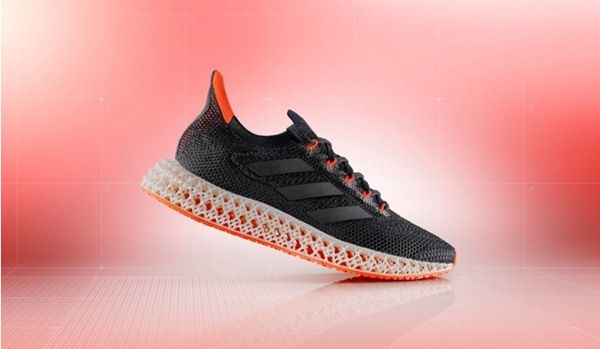
△4DFWD Sneakers
Shock absorbing mesh in the 3D printed OECHSLER backpack
Since 2017, OECHSLER is one of the global pioneers in additive manufacturing and its additive solutions have been inspiring prestigious customers from various markets. Now, OECHSLER has developed a new generation of hiking backpacks using industrial-scale 3D printing technology and BASF's high-performance Ultrasint ® TPU01. The main goal was to enhance the hiker's carrying experience by replacing the traditional foam-based back pad with a 3D printed lattice comfort element. The result is a hiking backpack that meets the needs of outdoor enthusiasts. In addition, OECHSLER meets the hiker's desire for a sustainable lifestyle by using 100% recycled materials.
To achieve this shock absorption, the backpack has a unique grid structure. The technology used in this case is HP's MultiJet Fusion, and BASF Forward AM's Ultrasint® TPU01 material. This honeycomb design and its placement in the backpack allows for cushioning between the back of the pack and the wearer. In addition, the elastic material was chosen to provide the high strength, flexibility and durability of the parts while maintaining good surface quality.
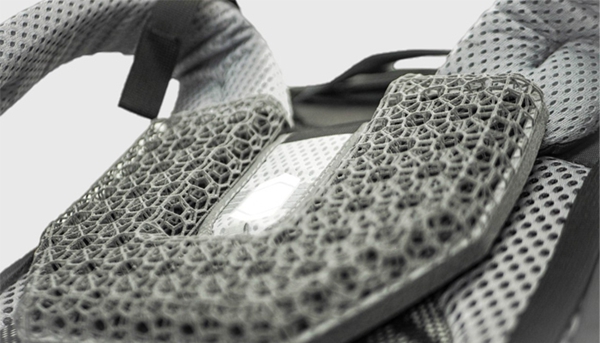
The lattice structure of the △ shock absorbing mesh (Photo credit: OECHSLER)
The story behind the back
The design of the hiking backpack, which is more ergonomic, lighter and uses less material than a real pad, was inspired by Dr. Leonhard Klein, OECHSLERAG's additive manufacturing project manager. He used his summer vacation to go hiking, and after hours of wandering, his shirt got soaked in the carrying area of his backpack. As usual, he changed his shirt and continued on his way.
Even with very high quality equipment, the unpleasant wearing comfort was still present in the area where the backpack and body meet. Other hikers seemed to have the same problem, as it proved during a break in the hut. Back at the office, he took a closer look at this supposedly unavoidable problem.
What should the perfect carrier look like in order to minimize the feeling of warmth and friction in the carrying area? After that, the OECHSLER additive manufacturing team set about redesigning the traditional back pad. Various analyses regarding pressure points were dispensed with to establish the perfect geometry and begin file programming as well as the first print tests.
A few weeks later, they were able to wear test the first printed back pad, including the belly band: and felt a huge improvement.
Unprecedented functionality for great comfort
The fully integrated cushioning experience unleashes superior comfort thanks to a freely designable lattice structure that can only be achieved using additive manufacturing. 3D printed back pads and hip fins have an open-cell structure that greatly enhances air circulation and minimizes heat buildup, resulting in significantly lower temperatures (3 to 5 degrees Celsius) and increased relative humidity in the contact area of the hiker's back. In addition, the maximum and average contact pressure is significantly reduced. The damping characteristics of the lattice structure can be adjusted by lattice geometry, strut thickness and lattice size. This allows different areas of the lattice to have different degrees of stiffness, thereby increasing the damping characteristics and comfort.
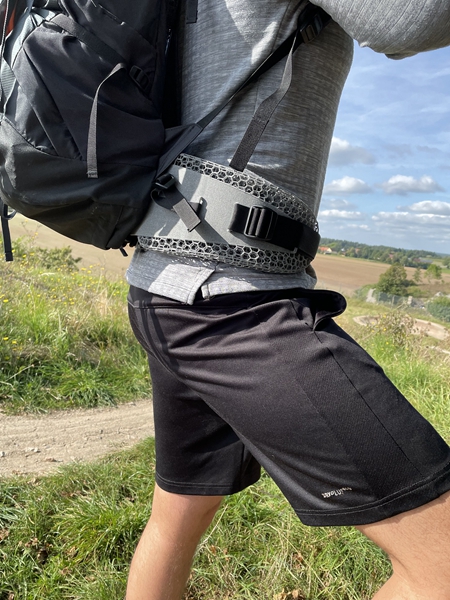
The four different examples below showcase OECHSLER's versatile materials and design options, which offer unlimited flexibility in terms of function, comfort and visual appeal.
Driven by a philosophy of providing our customers with greater production flexibility and efficiency, OECHSLER enables small as well as large volume production and complex components. The special Ultrasint ® TPU01 material is a multi-purpose TPU with strong, flexible and very durable part properties and excellent surface quality.
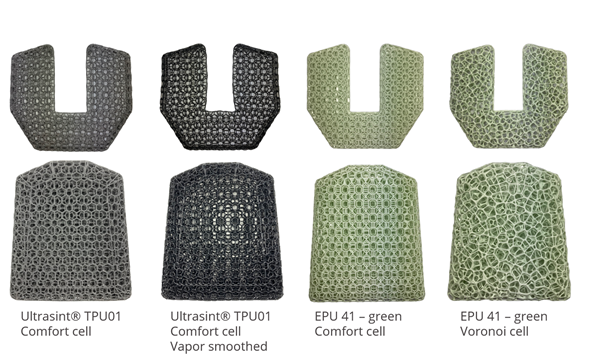
In addition, the material is very easy to print, has high process stability and is one of the highest yielding flexible materials in the 3D printing market. As an additional material option, Carbon's EPU 41 is a production-scale elastomeric material that is particularly well suited for elastomeric lattices that require high flexibility. The duration of a print run depends on the lattice structure and is therefore highly variable.
Sustainability
Thanks to the design flexibility offered by additive manufacturing, dorsal pads and hip fins can be produced in single pieces, resulting in fewer assembly steps, assembly times and ultimately significant cost reductions, eliminating the need for gluing or sewing. In addition, the unprocessed Ultrasint® TPU01 powder can be fully reused in subsequent print jobs. In addition, printed parts are 100% recyclable at the end of their life cycle. This makes the OECHSLER printed hiking backpack elements a completely sustainable solution.
Summary
OECHSLER offers customized hiking backpack printing solutions, including a full range of services from development to global production. The hiking backpack creates a new carrying experience with its integrated 3D printed mesh comfort pad. Some of the key benefits for customers are summarized below.
Maximized air circulation
Significantly lower temperature (3 to 5 degrees Celsius) and higher relative humidity in the contact area of the hiker's back
Reduced maximum and average contact pressure
Damping characteristics can be adjusted by varying the stiffness of one component
Infinite design flexibility
Easy and fast assembly
100% recycled print material