3D printing is an emerging manufacturing technology that uses digital models as the basis for stacking materials layer by layer to create physical objects. This technology will have a profound impact on traditional processes, production lines, factory models, and industry chain combinations, and is a representative disruptive technology for manufacturing. With the release of the EU 3D printing standardization roadmap, the development of a series of standards on 3D printing by international organizations, and the introduction of a series of specifications such as the U.S. FDA's technical documents on 3D printing, 3D printing gradually has its own common language and direction.
The application of 3D printing technology in medical device R&D and manufacturing has continuously empowered the development of medical device innovation, resulting in the formation of "3D printed medical device" products, which have been widely used in the past five years. 3D printed medical devices mainly use metals, polymers and other materials to achieve personalized customization and precision microstructure manufacturing. However, 3D printing brings "personalization" but also brings unique risks, traditional regulation of standardized products may be difficult to apply, while the lack of analysis and evaluation methods and standards for the process, quality and risks of 3D printed medical devices, making the regulation of 3D printed medical devices face many challenges. This makes the regulation of 3D printed medical devices face many challenges.
Establishing certification standards, regulations and evaluation systems for medical 3D printing products
In order to realize the later industrial application of medical 3D printing products, all relevant organizations should cooperate and the superstructure needs to play a key leading role.
The first breakthroughs in medical 3D printing occurred in orthopedics and dentistry, and are maturing in these fields. As a result, regulations for 3D printed medical implants were proposed for orthopedic and dental products back in 2010.
Currently, the State Drug Administration has approved four standard products for 3D printing for clinical applications. The State Drug Administration prioritizes their use in mature or proven areas, such as orthopedics and dentistry, with components for custom products manufactured by different provinces.
Because additive manufacturing products include custom products, the State Drug Administration plans to establish a complete evaluation system. Currently, the State Drug Administration has developed 40 guidelines on obtaining medical device registration certificates, of which seven principles are related to additive manufacturing. In the future, relevant standard systems, regulatory systems, guidelines, registration technical documents and fiduciary standards systems will be established to focus on developing clinical applications and making breakthroughs.
China's "Supervision and Administration of Medical Device Production" lists the safety and effectiveness of medical devices as the primary requirements. Currently, the U.S. Food and Drug Administration (FDA) mainly relies on reasonable rulings and valid scientific basis to control risks and ensure that medical products can be safely and effectively applied to improve public health. For new medical devices in additive manufacturing, regulatory science needs to be established to verify the performance of registered products. Important pre-registration tasks include conducting multicenter clinical trials and medical studies, and manufacturing products that have been summarized and peer-reviewed and published in scientific publications to provide an important basis for clinical practice. Such studies and production will facilitate the development of innovative products and facilitate the monitoring of the entire use process during the clinical application of the product.
The Institute of Medical Device Regulatory Science at Sichuan University is the world's first academic institution dealing with medical device related regulatory affairs with a mission to establish regulatory science for medical devices through pre-validation and risk control. This regulatory science should cover the entire life cycle of medical products based on background information from users, product developers and corporate risk control.
There are differences between domestic and international regulations developed for customized products. In the UK, the core regulatory philosophy regarding custom devices is as follows: except for material-related matters, the entire manufacturing process of additive manufacturing is the responsibility of the surgeon, including computerized tomography (CT) or magnetic resonance imaging (MRI) image data acquisition of the clinical patient, manufacturing, clinician validation, and subsequent clinical application.
The focus of our companies is to obtain a registration certificate from the State Drug Administration prior to marketing. The current situation in the UK suggests that China should issue clear registration guidelines for customized medical devices as soon as possible and accelerate clinical translation. Relevant registration guidelines should balance technical feasibility with the creation of practical benefits for all parties - especially patients. The reproducibility of medical additive manufacturing and the characteristics of the finished product (whether for human, animal or cellular models) must be achieved in a standardized manner. This topic deserves further reflection and exploration in future R&D and clinical applications.
All new technologies and novel materials - especially the three classes of 3D printed medical products - need to be systematically evaluated and approved by regulatory agencies prior to clinical application. Medical additive manufacturing technologies are still in the beginning stages of exploration. There are still several challenges to overcome in the clinical application of 3D printing technology in orthopedics and dentistry: unclearly defined risks and responsibilities, and long clinical registration and approval times. This is because it is difficult to assess the expected clinical effects of such products, especially for products manufactured by 3D printing. In addition, product quality control systems are not yet well established. Although clinical studies initiated by preclinical scientists are not intended for clinical registration, the associated management processes and quality control systems must meet the appropriate surgical medical requirements.
Quality Control Points for 3D Printed Medical Devices
For the performance of 3D printed medical device products, safety is the most important aspect. The quality control of 3D printed medical devices involves many aspects of the manufacturing process and production management, including medical-industrial interaction, raw material quality control, printing equipment management, processing process parameters, post-processing process management, and finished product quality control, each of which has different quality control points.
1 Medical-Industrial Interaction
Medical-industrial interaction is one of the prominent features of patient-matched 3D printed medical devices that differ from non-customized medical devices, in which the normality, effectiveness of interaction information, close cooperation and well-documented documentation appear to be very important. The key aspects of the whole process of medical-industrial interaction and its constituent elements should be accurately defined, and how to implement effective control of these elements should be studied.
The Guidelines for the Technical Review of Registration of Passive Implantable Bone, Joint and Oral Hard Tissue Personalized Additive Manufacturing Medical Devices (No. 70 of 2019) also specify that the products therein should meet the requirements of six aspects of medical-industrial interaction, including the design software? Printing equipment? Raw materials? Printing process validation? Post-processing methods and validation? Product testing, and requirements from personalized design? Product delivery and product use of three aspects of additive manufacturing medical device medical-industrial interaction capabilities to confirm.
2 Raw Material Quality Control
The quality control of raw materials is the basis for ensuring the quality of printed products, and their purity and performance are even more critical. The main raw materials involved in current additive manufacturing medical devices are metal powders used for 3D printing, including medical titanium alloy, medical pure tantalum and medical nickel-titanium alloy.
Metal 3D printing raw materials are in the form of spherical powder, so it is important to characterize the raw materials in terms of roundness, sphericity, fluidity, vibrational density, and loose packing density, and to verify whether their physical and chemical properties meet the requirements of medical device production. In addition, for the use of 3D printing recycled old powder, the manufacturer is required to explain and verify the mixed powder, verify the impact of the printing environment on the powder, demonstrate process stability and clinical acceptability, through these circumstances to determine the potential impact of powder recycling on the process and results of printing, otherwise the use of recycled powder material is not allowed.
3 Print Equipment Management
Printing equipment is an important piece of hardware that enables the production of 3D printed medical devices. The stability of the equipment operation and the stability of the printing process determines whether the batch-to-batch variation of the product is within acceptable limits. The printing parameters of the printing equipment should have a strict validation procedure to ensure the achievability and stability of the printing process. The reasonableness and effectiveness of equipment modifications should also be verified.
4 Process verification and post-processing process management
The initial printed product is subject to necessary post-processing, such as thermal stress relief, surface roughness treatment, and powder residue removal. These post-treatments are important to ensure the reasonable mechanical properties and biocompatibility of the product. At present, the standard "medical additive manufacturing powder bed melt forming process metal powder cleaning and cleaning effect verification method" is in the approval stage, mainly for "residual metal powder cleaning process" and "cleaning effect verification method" which Two aspects of the technical content to establish standards. Manufacturers can be implemented according to the provisions of the cleaning process and prove cleaning compliance.
5 Finished product quality control and product application risk assessment
In addition to meeting performance requirements after manufacturing, 3D printed medical devices also need to consider the potential health effects when interacting with the human body. In the case of 3D printed titanium implants, for example, for the evaluation of metal ion precipitation, the Institute has developed the "Evaluation Method for Metal Ion Precipitation of 3D Printed Titanium Implants for Additive Manufacturing Medical Products", which has been submitted for approval. The standard specifies the shape of the sample used for testing, as well as the metal ions to be detected (Ti, Al, V and impurity elements Fe).
Other concerns include the control of physical properties (mechanical and fatigue properties), chemical properties (control of chemical composition, microstructure) and biocompatibility. Biocompatibility should be evaluated comprehensively in accordance with the requirements of the GB/T16886 series of standards.
A series of policies to promote the integration of 3D printing technology and the real economy
In February 2015, the Ministry of Industry and Information Technology, the Development and Reform Commission and the Ministry of Finance jointly issued the "National Additive Manufacturing Development Promotion Plan (2015-2016)", proposing that by 2016 China should initially establish a more complete additive manufacturing industry system, and the overall technical level should be kept in line with international standards.
In May 2015, the State Council issued the "Made in China 2025" plan, which clearly puts the additive manufacturing industry as the focus of development and promotes the R&D and application of 3D printing technology and equipment in China. As an important element of smart manufacturing, 3D printing technology is mentioned in several plans of "1+X" of Made in China 2025. Related 3D printing companies will also be supported by a special national listing system.
In December 2016, the Ministry of Industry and Information Technology approved the National Additive Manufacturing Innovation Center, which was established by five universities - Xi'an Jiaotong University, Beijing University of Aeronautics and Astronautics, Northwestern Polytechnic University, Tsinghua University and Huazhong University of Science and Technology - and 13 key enterprises in equipment, materials, software and R&D to carry out common technology research, standard development and industrialization of 3D printing. At the same time, the State General Administration of Quality Supervision, Inspection and Quarantine approved the Wuxi City Product Quality Supervision and Inspection Center to prepare for the establishment of the National Additive Manufacturing Product Quality Supervision and Inspection Center to carry out related product testing, certification and other services.
In November 2017, the Ministry of Industry and Information Technology and 12 other departments issued the "Additive Manufacturing Development Action Plan (2017-2020)", which clearly proposes that by 2020, the annual sales revenue of China's additive manufacturing industry will exceed 20 billion yuan, with an average annual growth rate of more than 30%. 3D printing technology development requires materials, process equipment, core components and other The development of 3D printing technology requires the improvement of key technology research and development and industrialization capabilities, as well as the promotion of innovative applications in key industries.
The action plan for the development of medical 3D printing technology clearly direction, improve the quality and process performance of medical additive manufacturing materials, improve the material design and microstructure design technology for personalized medical devices, improve the quality performance and reliability of additive manufacturing equipment and core components, at the same time, to actively explore the "3D printing + medical" Demonstrate the application of new models for personalized medical devices, rehabilitation equipment, implants, soft tissue repair and other needs in the medical field, promote the improvement of personalized medical additive manufacturing products in the classification, clinical testing, registration, market access and other aspects of policy and regulations, research to determine the medical services of medical 3D printing products and services and medical insurance payment standards. At the same time, to establish and improve the additive manufacturing standard system, testing and certification system, and talent training system.
3D printing medical device registration technical specifications to open up a channel for market access
The clinical use of 3D printed medical devices has been restricted by regulations and policies, and there are no relevant standards for approval and registration in various countries. most 3D printed products mainly include clinical auxiliary products such as tumors, organ models and surgical guides, which only need to be filed and are not within the strict regulatory scope of approval and registration. in 2017, the U.S. Food and Drug Administration (FDA) issued the 3D Printed Medical Devices Technical Guidance" to regulate the manufacturing activities of related products, clarify the additive manufacturing process for medical products and the operational specifications for related testing, and put forward specific technical requirements for the basic processes of 3D printing such as methods, design, workflow, manufacturing processes, material control, post-processing, testing, and quality management, which provide a basis for the approval and registration of 3D printed medical devices and open up a market access for products The basic process of 3D printing medical devices
The basic process of 3D printing medical devices Enlarge image
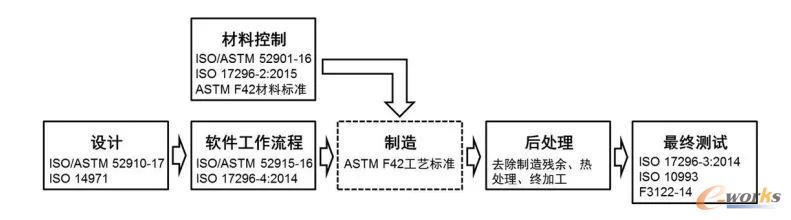
The basic process of 3D printing medical devices
In February 2018, the State Food and Drug Administration (CFDA) issued a draft of the "Guidelines for Technical Review of Registration of Customized Additive Manufacturing Medical Devices" for public comment, which clarifies the operation and information requirements related to registration and approval, and puts forward specific requirements for the use, product performance, clinical trials, and quality management of 3D printed products, with special emphasis on the conditions and capability confirmation of medical-industrial interaction, and the The production and validation process of 3D printed medical devices, including the testing of printing equipment, processes, post-processing, raw materials and final products should be strictly controlled, and the qualifications and capabilities of personnel for design development, product delivery and product use should be confirmed to ensure the safe and effective use of 3D printed products in the clinic, in addition, it is emphasized that a database should be established on the health status of patients during the whole life cycle of the product, the Evaluate the durability of devices and the traceability of medical incidents. The introduction of this approval and registration specification means that China's medical 3D printing industry will soon have formal technical review guidelines to remove barriers to the registration, approval and marketing of
Outlook
In general, "3D printing medical device standardization" can be divided into three concepts: 3D printing, medical devices, and standardization. 3D printing is the technology of manufacturing products, medical devices are products, and standardization is to make products meet the requirements. Only products that meet the requirements can be practically applied to achieve the meaning of the product.
For now, based on the systematic and extensive nature of standardization work, to continue to promote the standardization of 3D printing medical devices, it is necessary to promote many aspects simultaneously, including: 1) promoting the industrialization process of China's additive manufacturing technology; 2) strengthening the communication and cooperation between China and other countries and organizations in standardization work; 3) constructive suggestions from all parties in the field for the establishment of relevant regulations by Chinese regulatory authorities; 4) constructive suggestions from all parties in the field for the establishment of relevant regulations; and 4) constructive suggestions from all parties in the field for the development of 3D printing medical devices. 4) technical support from all parties in the field for the development of special risk analysis, risk control and other regulatory guidelines; 5) further establishment of standards for technologies and methods, raw materials, equipment and processes by regulatory authorities.
It can be seen from this, industry and standards are interdependent, industry can not be separated from the guidance of the standard, and the standard can not be separated from the industry to become a building in the air. Secondly, production, education, scientific research, testing institutions, medical units, standardization institutions, regulatory departments are all important components of this field, and all parties achieve synergy and integration in function and resource advantages according to different divisions of labor to jointly promote the development of standardization of additive manufacturing medical devices.
In the "2020 National Medical Device Safety Awareness Week", the FDA has demonstrated the eight dimensions of quality control formed by the latest components of the evaluation of additive manufacturing medical device products, including performance and characteristics, which are divided into three major categories at the broad level, namely product-based, manufacturing-based, and user-based approaches. A relatively integrated and systematic approach to ensure the quality of 3D printed medical devices and meet user needs.
These can be used as entry points to help medical device companies better understand the seemingly complex work of standardization from the ground up. There is an old Chinese saying "respond to all changes with no change", which is reflected in the standardization process: although the product is individualized, the workflow and operation can still be standardized, and a standardized process can be used to regulate a variety of individualized products. Understanding these concepts, coupled with continued familiarity with regulatory compliance and 3D printing technology, allows companies to better innovate their products based on standardization requirements and truly use new technologies to bring new products and meet approval requirements.
Expanding product development to a longer process, from experimental research to production applications, even in the lab, for 3D printed medical devices, should make the awareness of industrialization and clinical translation an important principle throughout the R&D process, and not just let the product stay in the research phase just for the sake of publishing papers. Similarly, the requirement for medical device companies to move from the scientific research to the industrial stage is that when a 3D printed medical device product is developed, obtaining regulatory approval and certification cannot be the ultimate goal. Product certification is only the beginning of the application, and the effectiveness of the application is the ultimate pursuit of medical device products.
For the future development of 3D printed medical device regulation and standardization, "quality" and "risk" will continue to be the two key words to explore in this field, and the first task is still to establish a better guideline, standard and regulatory system. The construction of a standardization and regulatory system for 3D printed medical devices has been listed as one of the important tasks and plans during China's 14th Five-Year Plan. These systems can be expanded horizontally to cover a wider range of technologies and products, and vertically to extend and improve the details of specific products and technologies.