On May 28, 2022, GLOBE NEWSWIRE announced the release of the report, "Global 3D Printed Medical Devices Market Analysis Report 2022". The report features data from, 3D Systems, EnvisionTEC, Stratasys Ltd., Arcam AB, Cyfuse Biomedical, materialise NV, Organovo Holdings, EOS GmbH, FabRx Ltd. and Concept Laser.
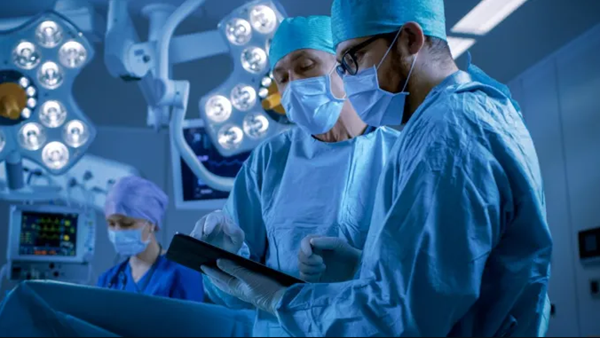
△Diagram of the future outlook of 3D printing in the medical device market
Market Analysis Overview
The global 3D printed medical devices market, is expected to grow from USD 2.29 billion in 2021 to USD 2.76 billion by 2022, at a compound annual growth rate (CAGR) of 20.4%. The market is expected to grow at a CAGR of 13.0% to US$4.49 billion by 2026.
The market includes, among others, the sale of 3D printed medical devices and related services. 3D printing is the process of creating three-dimensional medical devices with the help of computer-aided design. Some 3D printed medical devices, include orthopaedic and cranial implants, surgical instruments, dental restorations such as crowns and external restorations.
The main types of 3D printed medical devices are implants, surgical instruments, prosthetics and tissue engineering devices. The technological advantage allows medical implants with complex geometries to be manufactured using 3D printing.
These consist of raw materials such as plastics, bio-ink, metals and alloys. technologies involved in 3D printing medical devices include fused deposition modelling, digital light processing, stereolithography and selective laser melting.
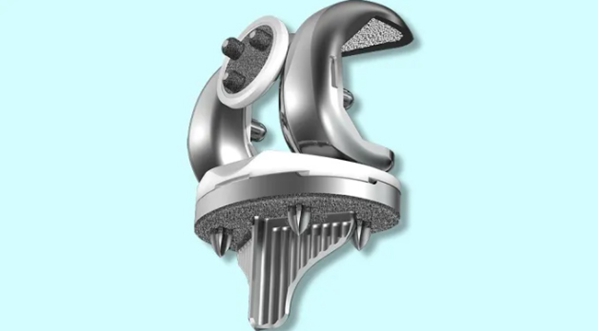
△Stryker uses 3D printing technology to facilitate the bonding of bone to implants and to reduce post-operative recovery time
Overview of application prospects
The technology is suitable for use in orthopaedics, spine, dentistry, hearing aids and other end-users (e.g. hospitals, diagnostic centres, academic institutions, etc.).
The increasing growth of osteoarthritis and similar musculoskeletal disorders is one of the main factors driving the growth of the 3D printed medical device market. Osteoarthritis, a disease that damages the cartilage and surrounding tissues of joints, causes pain, stiffness and loss of joint function in people.
3D printed medical devices, which can help patients create replicas of their joints, can also provide surgeons with critical information that may not be visible in a 2D scan. According to one report, the global chance of developing osteoarthritis increases as people get older.
For example, a report from the US National Library of Medicine reports that by 2040, approximately 78 million (26%) of US adults aged 18 and older, are expected to suffer from arthritis. For this reason, the future will further drive the development of 3D printed medical devices, which will have a positive impact on market growth.
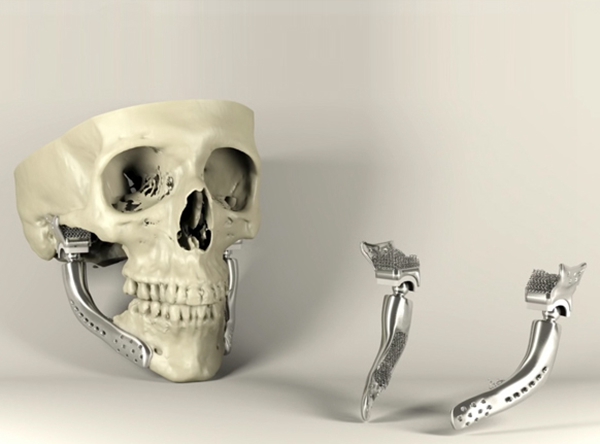
△Metal 3D printing for jaw reconstruction treatment
Problems encountered so far
Biocompatibility issues associated with 3D printed medical devices are limiting the growth of the 3D printed medical device market. Biocompatibility means properties that make a material or device compatible with the human body. If a 3D printed implant is not biomechanically compatible with the patient, then the patient may experience side effects such as abnormal bone growth and bleeding. Currently, the most common material used in the manufacture of 3D printed medical devices is the metal titanium.
Although titanium offers reliability and accuracy in the manufacture of medical grade 3D printed constructs, there is a segment of the population that rejects the element, mainly due to the chemical composition, which inhibits the interaction of bone and tissue with the implant. In addition to this, there is a subset of reasons that can lead to implant failure, such as high stiffness, high corrosion rates, toxicity or infection due to exposure of the bone to infected metal implants and consequently.
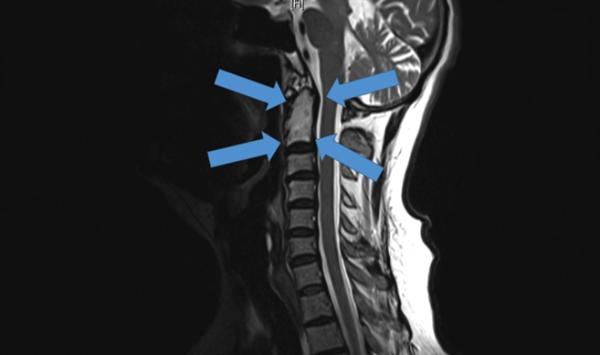
The world's first 3D printed vertebral implant at the end of 2015
Latest trends
The spine industry is also one of the latest trends in the future medical device market. Innovative products can be achieved through 3D printing technology that promotes inward bone growth and improved fixation of the implant to the spinal bone, shortening the manufacturing process, increasing patient satisfaction and, in some cases, making it more cost effective.
An example is Medtronic's titanium 3D printing platform, TiONIC technology. Using a laser method to manufacture implants with enhanced surface texture, Artic-L is the company's first metal implant to be manufactured using TiONIC technology. It can be used by surgeons in spinal surgery. There is also K2M's Lamellar, which also uses titanium to manufacture 3D spinal implants. One of the unique advantages of using metal 3D printing technology is that it allows for structures that were once considered impractical by traditional manufacturing techniques.
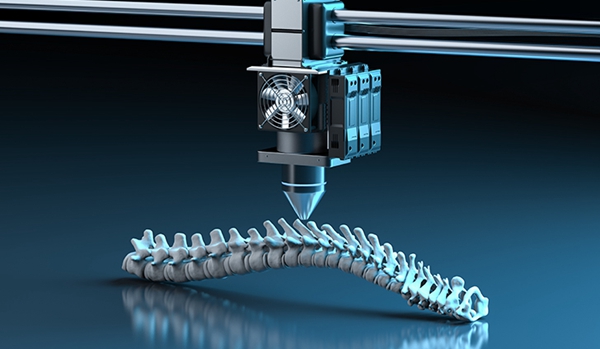
Spine companies such as Tsunami Medical, SeaSpine and Osseus use 3D printing to create spines
About industry certification developments
The Food and Drug Administration (FDA) has a Centre for Devices and Radiological Health (CDRH) to regulate companies that manufacture, repackage, relabel and/or import 3D printed medical devices in the U.S. The FDA provides guidance recommendations to manufacturers that include device design, manufacturing and testing considerations during the development of 3D printed medical devices.
The recommendations require manufacturers to assess the biocompatibility of the final finished device in accordance with "International Standard ISO-10993, Description. It also requires manufacturers of 3D printed devices to include additional information on the labelling of any toxic chemical additives (such as certain additives, catalysts, adhesives and curing agents, uncured monomers and plasticisers) used in the manufacture of 3D printed medical devices.