Introduction: For decades, German automotive companies have been promoting the use of 3D printing in car manufacturing. Many companies have dedicated laboratories and have been conducting large-scale research and product development for many years. They have built up an insurmountable technological advantage by partnering with those established service and 3D printing original equipment manufacturers (OEMs), as well as the Fraunhofer Institute in Germany. In addition, many of these companies have begun to make extensive use of 3D printed parts in F1 and bespoke high-end automotive customisation, taking full advantage of the manufacturing benefits of 3D printing. In the US and Asia, 3D printing for car manufacturing is still relatively weak. Recently, however, we have seen the emergence of a new "dark horse" in this field of application - General Motors, which, despite being one of the two largest car manufacturers in the world, is making a splash with its entry into 3D printing technology.
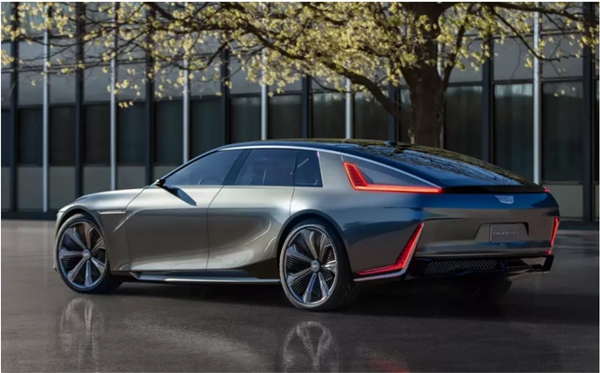
Starring on 27 July 2022, GM recently announced that it has used 60,000 flexible 'spoiler closure seal' parts made using HP's MJF technology for the 2022 Tahoe model. The company is producing these parts using GKN's Forecast 3D unit and BASF Forward AM Ultrasint TPU 1 material. GM also relied on AMT's vapour smoothing technology to complete the parts.
Refreshingly, GM is showing the world a case of using 3D printing to make a vehicle bridge, a flexible part that is not in fact what additive manufacturing specialises in. The company has also announced that it will install more than 100 3D printed parts, both metal and polymer, in its new Cadillac CELESTIQ model. It has invested $81 million to build the car at its Global Technology Centre for Additive Industrialisation. There is no doubt that GM's bid for 3D printing supremacy will make the Germans work harder. German car companies such as Mercedes, BMW and Volkswagen tend to be more focused on in-depth technical and process knowledge. For years they have been working on materials, automation, post-processing, qualification methods and so on. In contrast, General Motors was a late entrant to the 3D printing business, having started around 2020 and ordered 60,000 additive parts from a service. As you can see, the German company has more in-depth knowledge of additive manufacturing, but if GM can rely on outsourcing services to get additive parts and get a head start on press, then that's not a bad way to go.
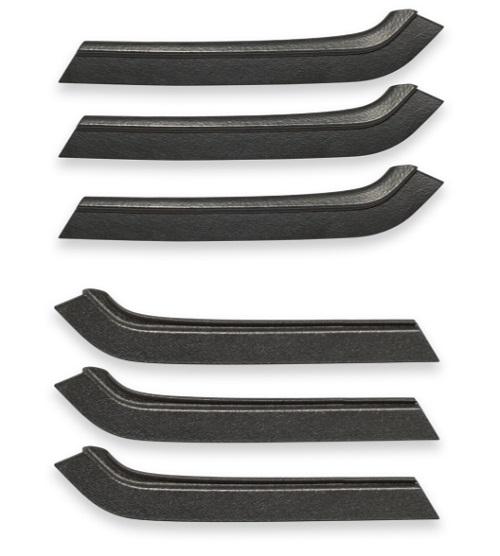
3D printed automotive parts without powder bed fusion technology
Similarly, SOLIZE is using HP systems to make parts for Nissan's NISMO car. This could mean that we could see other car manufacturers without much background in additive manufacturing quickly rolling out components through the service.
Germany's huge investment in powder bed fusion has also slowed their adoption of 3D printing and has made the technology unnecessarily expensive. Powder bed fusion additive technology has a large profit margin in terms of materials and machines, as well as a very high cost base. It is also very complex, which means that it will take companies several years to deploy it. As it is a complex technology that looks ready for use in factories, the company invested several years in industrialising it. This led to many automotive applications in Germany staying behind the scenes for a long time.
Now, using adhesive injection technology, much lower part costs can be achieved, especially with a high degree of automation. Only software is required to qualify the parts and the technology is best suited to series production rather than many unique parts, although of course there is also great potential for customised parts. Bound metal 3D printing with simple material extrusion systems can also provide low-cost parts for certain geometries, and I'm sure Markforged and BASF will push this type of technology further.
Meanwhile, some higher performance polymers, particularly polyamides, could further drive the penetration of 3D printing in automotive components. This could yield very significant cost benefits if the automotive industry uses reliable material extruders to manufacture parts. The significant investment in powder-bed molten metals and polymers should also lead to the mass printing of some new parts.
Where will automotive parts be 3D printed?
Aspiring manufacturing service platforms, such as MakerVerse, can further deploy parts without the significant capital required by services such as Morf3D, Azoth3D and Sintavia. However, where does the future lie for 3D printing in automotive components?
From prototypes to end-use parts, now seems to be the right time. In fact, we expect more companies to use 3D printed automotive parts in the future, but the modus operandi may not yet be certain: will they print them through a service? Or will they ask their existing Tier 1, 2 and 3 partners to print these items? While car manufacturers have the knowledge and experience of 3D printing, their suppliers currently do not. Nor do these suppliers have much room financially to make a deep and imaginative investment in 3D printing.
So, will car companies 3D print their own parts? For some of these components, it is possible. Manufacturers could offer high-value, customised products and make all the profits from them. They can make bridges quickly if they can afford to, or create new models in-house, but the operational model for 3D printing of automotive parts remains to be seen.
Which automotive parts will be 3D printed?
The question of which components will be manufactured for the automotive industry using 3D printing will also be a difficult one. We have already seen custom SLA components, titanium components, FDM components, visible, hidden and lightweight parts, and parts with integrated functionality. Everyone is playing with different materials, technologies and applications.
In addition to jigs and fixtures, tooling is an obvious area. Large-scale customised polymer parts also seem to be evident. In some cases we can also see integrated monolithic, lightweight components. Directed energy deposition (DED) and wire-arc AM-style processes for chassis and larger components will be very exciting, but applications seem a long way off.
The biggest opportunities lie in the maintenance, repair and overhaul (MRO) business for millions of automotive components worldwide, which is where basic performance enhancement projects on new vehicle platforms are being designed. In addition, we should be aware that there is still a huge gap between the cost of automotive parts made by other manufacturing methods and what the 3D printing industry is charging for their parts. We need to address this issue to make progress.
GM's CELESTIQ
The CELESTIQ is a limited edition car that GM will hand-build in its global technology centre. We often see 3D printing projects struggle because the people involved in production don't want to take the time to introduce new technology into the manufacturing business. Building this car by hand will allow GM to understand 3D printed parts and fit them to the car in a defined and closed manner.
In this case, additive manufacturing does not have to be in a position to completely replace the production path of the rest of the car company's models; it will only be done for parts on this particular range of cars. Importantly, if GM finds good results in using additive manufacturing to produce bespoke models, it might actually make some changes to car production in the future.
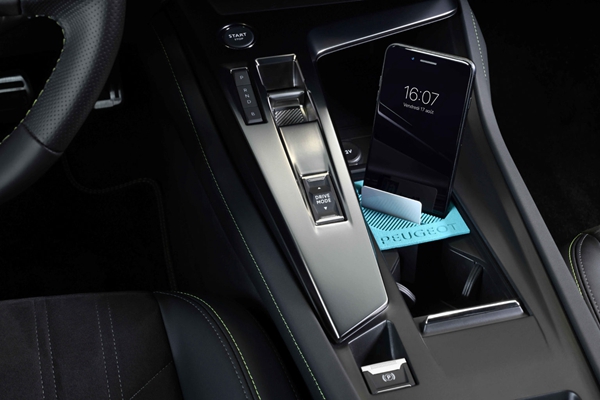
△ Peugeot's 3D printed mobile phone or card holder. Image courtesy of Stellantis.
Car companies make very little money on production cars, but on the expensive bespoke car line it's a different story. Manufacturers also have side businesses in building bespoke cars, such as the Bentley Mulliner, Porsche Individual and Mercedes Guard. these are all small batch but highly profitable.
Ideally, manufacturers might want to make customisation commonplace with high-volume, profitable, unique parts sold to millions of people. To do this, you need great confidence and institutional change. This scenario is ideal, but also extremely difficult to implement. Meanwhile, the ultimate bespoke car is a one-off concept car. It is a very expensive car, costing millions of dollars, but showing the future of design. The concept car is a technological toy that the whole world can see. Limited edition supercars, like those sold by other car brands, are priced at over $1 million.
So what if GM now started building small-batch, hand-built cars in-house all the time? The company reportedly wants to charge $300,000 for CELESTIQ. This could actually be very lucrative if the company uses 3D printing and complementary technologies.
Instead of losing money on a concept car, GM could also produce a limited number of usable working vehicles each year. These could be highly profitable for the company, while attracting journalists and car enthusiasts. These cars could create a halo effect for the brand in a manageable and profitable way.
Of course, it is not certain that this is the company's intention. celestiq could be a one-off test bed to familiarise itself with 3D printing models. But imagine the marketing launch points you could create by building completely crazy, drivable cars to showcase your brand in front of onlookers on the street. Imagine if customers paid upfront for your design exploration and inspired brand enthusiasm in the process. Imagine if you sold 300 cars a year to car collectors at $1.5 million each, finances would no longer be an issue and this approach could also make good use of 3D printing.
As well as being able to make a large number of moulds and tools, additive manufacturing is the key technology that would allow a company to produce a large number of parts for such a bespoke car. Imagine if CELESTIQ wasn't just a one-off, but a future approach that could create cheers, creative points and set world trends. Then for GM, at $300,000 a custom sports car, it would be the ultimate marketing tool,a cost effective marketing tool and a showcase to drive around.