Magnetic cores are magnetic materials in sheets with high magnetic permeability. They are commonly used to guide magnetic fields in a wide range of electrical systems and machines, including electromagnets, transformers, motors, generators, inductors and other magnetic components. To date, the 3D printingof magnetic cores has been a challenge because of the difficulty in maintaining their efficiency. However, a team of researchers has now proposed a comprehensive laser-based additive manufacturing workflow that it says could produce products superior to the magnetic properties of soft magnetic composites.
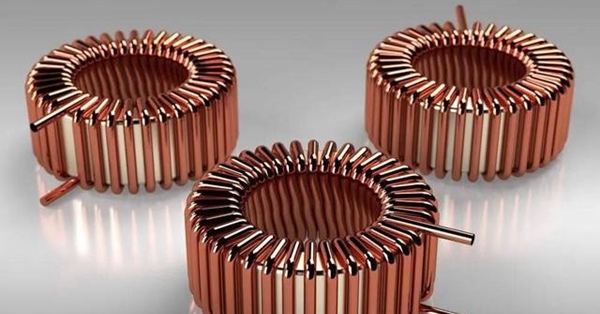
3D printing electromagnetic materials
Additive manufacturing of metals with electromagnetic properties is an emerging area of research. Several motor R&D teams are developing and integrating their own 3D printed components and applying them to systems where freedom of design is one of the keys to innovation. As an example, 3D printed functional complex components with magnetic and electrical properties can pave the way for customised embedded motors, actuators, circuits and gearboxes. Such machines can be produced in digital manufacturing facilities with less assembly and post-processing etc., as many components are 3D printed. However, the vision of 3D printing large and complex motor components has not been realised for various reasons. This is mainly because there are certain challenging requirements to be met on the equipment side, such as small air gaps for increased power density, not to mention the problem of multi-material components. So far, therefore, research has focused on more "basic" components such as 3D printed soft magnetic rotors, copper coils and aluminium oxide heat conductors. Of course soft magnetic cores are also a priority, but the most important obstacle to be addressed in the 3D printing process is how to minimise core losses.
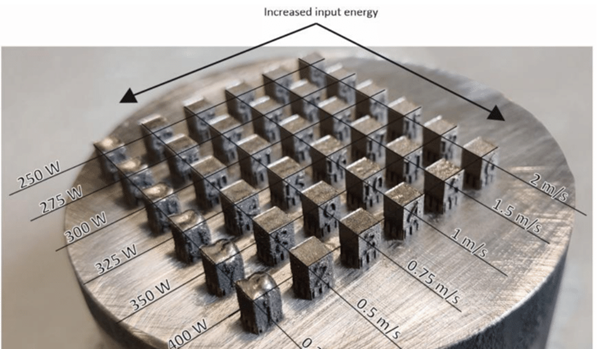
△ A set of printed sample cubes showing the effect of laser power and printing speed on the core structure. Image credit: Tallinn University of Technology
Optimised 3D printing workflow
To demonstrate the optimised 3D printed core workflow, the researchers determined the optimal process parameters for the application, including laser power, scanning speed, hatch spacing and layer thickness. And the influence of annealing parameters was investigated to achieve the lowest DC losses, quasi-static, hysteresis losses and highest permeability. The optimum annealing temperature was determined to be 1200°C, the relative density to be 99.86% at the highest, the minimum surface roughness to be 0.041mm, the minimum hysteresis loss to be 0.8W/kg and the ultimate yield strength to be 420 MPa. Ultimately, it was confirmed by the researchers that laser-based metal additive manufacturing is a viable method for 3D printing core materials that can be applied to electric motors. In future research work, the researchers intend to characterise the microstructure of the parts to understand grain size and grain orientation, as well as their effect on magnetic permeability and strength. The researchers will also further investigate ways to optimise the 3D printed core geometry to improve performance.
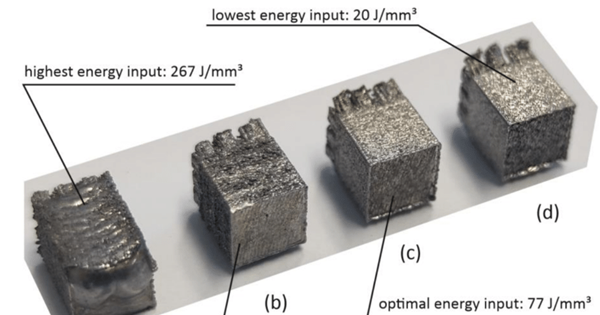
The effect of ∆ energy input on the surface roughness of 3D printed magnetic cores
The promise of combining 3D printing technology with magnetism
The combination of 3D printing and magnetism is inspiring a range of new applications, not just motors. Earlier this year, an international team of scientists led by the Cavendish Laboratory at Cambridge University used 3D printing technology to develop a set of miniature nanomagnets. Using a bespoke 3D printing process, the nanomagnets, which are shaped like a DNA double helix, show promise in areas such as particle capture, imaging technology and smart materials.
Elsewhere, researchers at Spain's interdisciplinary research centre, the IMDEA Institute of Nanosciences, have recently developed a new method for 3D printing magnets from recycled materials. This work was done to address supply chain issues during the global epidemic, where the lack of materials for manufacturing included those needed to make magnets.