Researchers at the University of Tehran have developed a new type of concrete that can be 3D printed into homes that produce 400 times less CO2 emissions than current construction. In simulated 3D printing of the home, the team found that using reactive magnesium oxide mixed with insulation and phase change materials (PCM) reduced its energy use and environmental impact. If deployed on a broader scale, the engineers say the material could help make 3D printing a more attractive tool for addressing housing shortages and climate change.
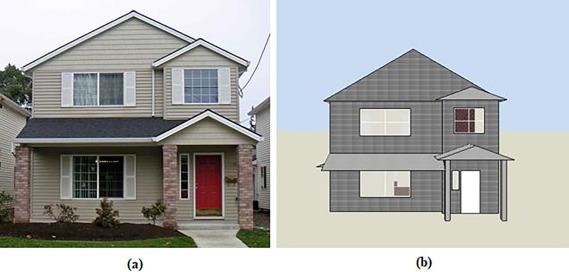
The team's DesignBuilder 3D printed house model. Image from Tehran University.
Carbon emissions from construction
According to a study by the European Commission, conventionally constructed buildings account for 36 percent of all CO2 emissions generated in the EU. Of course, affordable housing construction is necessary due to population growth, but building these homes more sustainably is quickly becoming a hot topic of research. These studies often revolve around reducing the cooling and heating loads of buildings.
Doing so is considered critical to improving the sustainability of the housing construction process, as it can help reduce the fuel demand associated with construction and heating. Previous research has found that one way to improve the thermal performance of such buildings is to use PCM for 3D printing, which can absorb a specific range of heat and manage internal temperatures.
However, the Tehran team says these PCMs have been shown to "increase thermal capacity," but their mechanical properties may be degraded, hindering their potential for end-use applications. The engineers also claim that other materials that have been injected into cement with geopolymer networks have had varying degrees of environmental success, some of which still have high CO2 emissions.
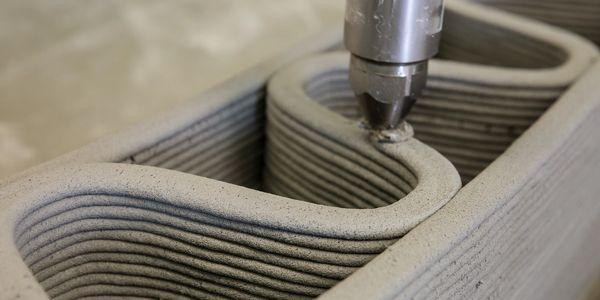
A concrete 3D printer in operation. Photo from Hamilton Laboratory.
3D Printed Houses Are More Sustainable
To determine the best cement formulation for the 3D printed house, the team studied the performance of a simulated building, achieved with magnesium oxide (RMC) and calcium sulfoaluminate (CSA) cement. Tests conducted with DesignBuilder software proved that both were able to set up quickly and showed high initial strength levels, but RMC had a higher compressive strength of 60 MPa. In analyzing the sustainability of this virtual two-story building, the researchers chose to perform a full life-cycle assessment (LCA) of it, from transportation to material and power use. The results of the LCA proved that both of their cement formulations had lower ecological impacts than traditional Portland cement, while the CSA had higher energy consumption than RMC.
To make their material more effective at controlling internal temperatures, the engineers later added calcium chloride to the mixture. Adding this compound allowed the mixture to be 3D printed into the concrete, absorbing and releasing heat as they reached their melting or freezing point. Supplementing the RMC with foam in the simulation also enhanced this effect, optimizing the building's insulation. Ultimately, it was found that the presence of magnesium increased the carcinogenic toxicity of the house walls, but that 3D printed RMC with insulation had minimal ecological impact. As a result, the team concluded that 3D printing could "significantly help reduce the energy consumption of future buildings," even though their RMCs were still very water-intensive and had toxicity issues that needed to be addressed.
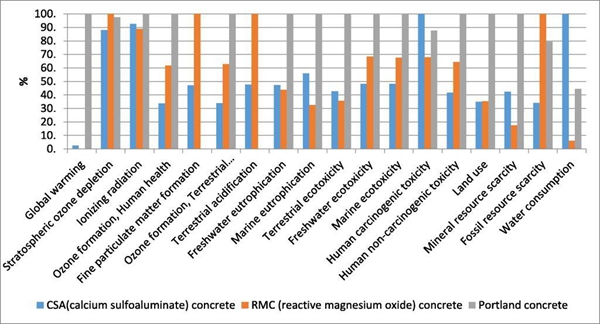
The researchers' LCA results. Image from Tehran University.
The potential of AM in the self-construction industry
A great deal of research is being done to optimize the thermal efficiency of concrete 3D printed buildings, especially in the area of construction materials. For example, researchers at Texas A&M University have developed 3D-printed phase change materials that can be used to build houses that can be passively thermoregulated internally. In the past, Microlight3D has also received support from the European Union to develop concrete for the construction of "self-cooling" buildings. As part of its Future and Emerging Technologies (FET) program, the company is working with five European universities to design a microstructured material that can combat the urban heat island phenomenon.
Elsewhere, teams at Swinburne University of Technology and Hebei University of Science and Technology have taken a different approach to making housing construction more environmentally friendly. By developing a 3D-printed material made from construction waste, the engineers hope to reduce carbon dioxide emissions from additively manufactured buildings and the technology's reliance on natural resources.