Introduction: The term "hypersonic" has got to gain new attention from people with the release of the U.S. government's report on unidentified aerial phenomena (UAPs), which are usually positioned at speeds above Mach 5. Whether you believe it's aliens or not, space competition between major powers has begun and, not coincidentally, pre-research and development toward a vehicle of unheard of speed and agility.
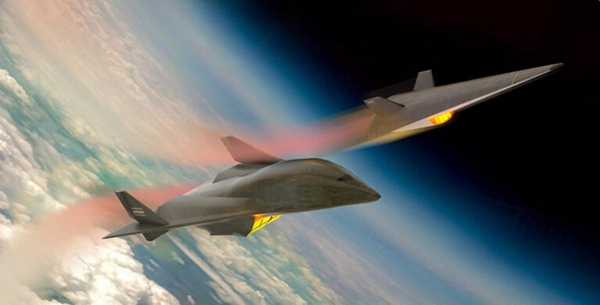
△ Artist-designed concept of future hypersonic aircraft. Meanwhile, propulsion systems with 3D printed parts are being developed to propel the vehicle to hypersonic speeds
Specifically, "supersonic" refers to an aircraft that breaks the sound barrier at Mach 1 (such as the now-retired Concorde and the soon-to-be-launched Rumble). Mach 5 would be equivalent to five times the speed of sound and more than 3,500 mph at sea level. But when the upper limit of this speed is reached, a hypersonic environment is entered.
Researchers at Purdue University, are exploring a new metal 3D printing technology through which they can produce fully dense end-use parts that are more robust than traditional casting methods. These parts can meet the conditions for applications in the demanding environment of hypersonic speeds.
Exploring the technical world of hypersonics
"Mach 5 is a difficult technological red line to cross," said Carson Slabaugh, associate professor at Purdue University. His 20-person team in the Zukrow lab has been working on high-speed combustion systems since he started his lab at Purdue in 2015." When a vehicle travels at high speeds, the air flowing around and inside the fuselage undergoes extreme compression and heating. At speeds up to Mach 5, the temperature increases approximately six times and the pressure increases several hundred times. At the same time, this thermal and mechanical loading leads to a complete change in the regime of aerodynamics, thermodynamics and structural mechanics."
Flying at speeds above Mach 5, this is when the air in the atmosphere is thousands of degrees hotter and hundreds of pounds more pressurized as it rushes by. If you fly fast enough, the air itself can even become chemically reactive. The extreme flow conditions are a technical challenge for any vehicle system that gets its thrust from burning fuel.
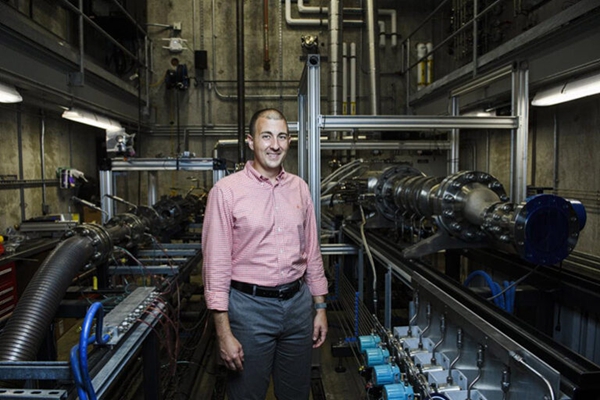
△ Associate Professor Carson Slabaugh in front of the combustion test stand in the Zucrow lab at Purdue University
Metal 3D printed parts
To address this challenge, Slabaugh and his team worked with VELO3D to print fuel injectors with complex geometries for extremely high fuel-air mixing performance. Conventional manufacturing methods are unlikely to produce such parts, especially under the extreme test conditions that require high-strength superalloy metals.
Through our collaboration, we helped Velo3D design the high-speed combustion system and, at the same time, they taught us how to make better use of 3D printing technology," Slabaugh said. That's the kind of mutually beneficial relationship we build with our industry partners as we address the challenges associated with the transition to advanced technologies."
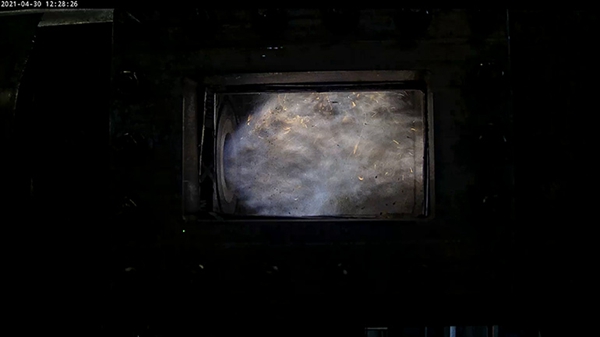
△ Flames in a test chamber that simulates a high-speed propulsion system in a hypersonic environment
Much of the research and development for the hypersonic vehicles they develop is supported by NASA and defense-level budgets.
Such advanced flight testing corresponds to high development costs, so the team wants to save as much money as possible, just like that facility at Purdue University, where Slabaugh's team is building a ground-up validation vehicle engine component is a test site.
We're designing components that will simulate operation in a hypersonic environment, while they don't need to go up or move and remain bolted to the ground at all times," Slabaugh said.
Methods such as computational fluid dynamics (CFD) and fluid-structure interaction (FSI) can be used to simulate the behavior of materials and structures in air or liquid flow. This allows engineers to optimize designs before anything is built.
Solving technical challenges
A fundamental problem is that we can't reliably predict the flow and flame conditions within the engine at hypersonic conditions," Slabaugh said.
He also talked about how the team went about solving this problem: "We worked with Velo3D to build a very large 3D printed combustor that will be used to create a hypersonic environment in a test cell on the ground."
In order to create a hypersonic vehicle on the ground, you have to build a rocket engine that has a large, converging divergent nozzle, and a supersonic plume of extremely hot gas. Then put whatever parts are being tested inside that plume.
Slabaugh said." With Velo3D, we designed the injector for this burner to produce a very specific turbulent flow field that mixes the fuel at a certain speed and allows us to stabilize a very powerful flame in a very compact volume. This sets the stage for all the things we're going to test downstream."
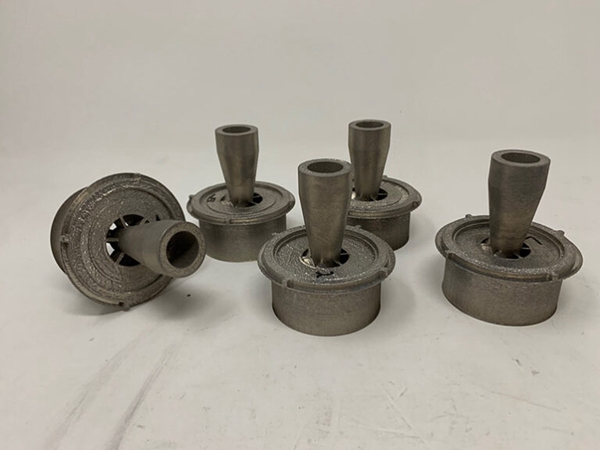
Δ3D-printed injector produces stable, powerful turbulent flames
To validate the performance of this 3D printed burner, the use of a high-strength, high-temperature super alloy made from Hastelloy X, which can withstand hypersonic environments, allowed the Purdue team to quickly determine which design would be most effective.
Engineers cleverly changed the flow paths of the injectors with five different designs. For 3D printing, it was simply a matter of adjusting the STEP data file. Meanwhile, the VELO3D Sapphire system's print preparation software has an auto-adaptation feature. As a result, the design was printed and passed the test conditions associated with hypersonic speeds.
In just two weeks, the team was able to filter out the best performing product, which had all the static and dynamic characteristics they were looking for. This high performance injector, met the key parameters of burner performance, flame power and flame stability that the engineers were most interested in.
The team's next step is to assemble a large array of injectors into a more powerful burner. Velo3D is in further consultation with Zucrow Labs to help them take advantage of 3D printing's "pay-as-you-go" capability to integrate the injector set into a single 3D printed component.
From there, engineers will continue to refine and assemble a complete combustor system, with the technology aiming for full hypersonic test capability by the end of 2022.