Introduction: 3D printing first appeared in 1980, but it's only now that the technology has become affordable enough to be used in the home. Whether you're a hobbyist or an artist looking to do something fun in your spare time, 3D printing is a manufacturing technology that you can experiment with at home. The technology also has many medical applications, from prosthetics and implants to dental braces, surgical guides and more, and Mohou.com lists some of the most promising uses for 3D printing in medicine today.
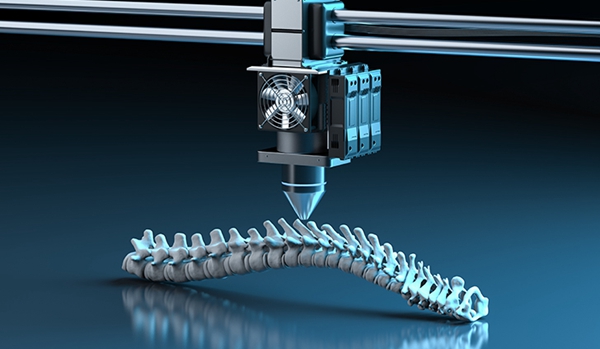
Implants
Implants are the most important use case for 3D printing technology. 3D printing has been used to create custom implants for a variety of medical conditions, such as knee replacements, dental implants, and even breast reconstruction. These implants are usually made from 3D printed clear resin, so they can be easily moulded to fit the exact shape of the patient's body. They also offer greater flexibility than traditional metal or ceramic implants, providing a better fit and movement within the body.
3D printing technology could also help children and adolescents by creating individualised treatment plans for children with scoliosis (curvature of the spine), enabling doctors to quickly create orthoses that fit the body perfectly, so they don't need invasive surgery or braces as adults.
In addition, researchers are investigating how 3D printers can be used for organ printing or to print limbs for amputees from soft materials such as silicone or rubber, which are more comfortable than traditional prostheses and can even allow the wearer to perform a full range of motion at all times without any external support, such as crutches or a wheelchair.
Prosthetic limbs
The WHO estimates that more than 30 million people need prosthetic devices, but most developing countries do not have adequate medical conditions. 3D printing can solve this problem. One of the most typical medical applications of 3D printing is the manufacture of prosthetic limbs. The technology is used to create prosthetic limbs for children who have been born with a congenital disability or have lost one or more limbs in an accident.
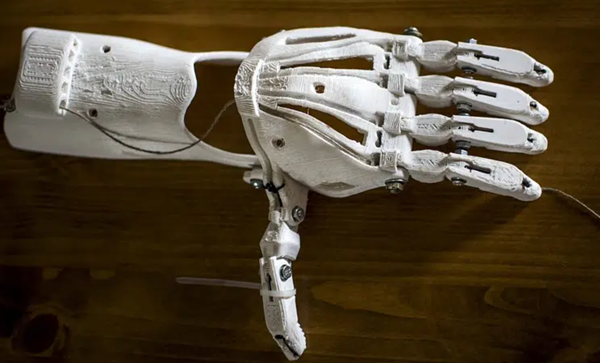
Prosthetic limbs are usually made from silicone and other materials that can be moulded. But because they need to fit perfectly, each new mould must be customised when it needs to be replaced. This process can take weeks or even months and is costly.
3D printing offers an alternative solution, making custom parts (of the same material as Lego blocks) directly from polymeric materials such as ABS plastic. To make such a part, you first design it on your computer; you then send the file to your printer and its supply of raw materials, which may include several different plastics if required. The 3D printer is then used to 3D print the manufacturing for the user.
Surgical models
3D printing has become a staple of medical applications. one of the most common uses of 3D printing is to create models of organs and tissues for use in surgical simulation, training and testing equipment. These medical models can be made from many different materials, including clay or wax, but as technology has advanced and become more economical, researchers have been able to print 3D replicas using digital data from a patient's CT scan or MRI image.
These replicas are often used by students learning how to perform surgery, practising before performing surgery on real patients. However, they are also useful in surgery itself: doctors can use these models as a visual aid when planning and performing surgery so that their team members know exactly what needs to be done when working inside the body.
There is another major benefit. These replicas can help doctors to test new drugs or devices before using them in real bodies, as it allows them to observe how something will affect different parts of the body without actually having to do so (which could lead to unnecessary injuries).
Devices
3D printing technology can also be used to create more customisable and cheaper devices. Using 3D printing, you can make devices specifically for patients, whereas traditional manufacturing means making millions of identical devices that may or may not meet your needs. Using this technology, instruments can be made that are more accurate than traditional manufacturing methods because they are designed specifically for the need, and they also tend to be more durable than other devices that are less customised in the manufacturing process.
Another benefit of custom-manufactured medical devices is their flexibility. With 3D printing, you can use materials such as rubber or plastic, which allow your devices to bend better than metal devices. It makes them ideal for handling soft tissues without causing too much damage to them.
Pharmaceuticals
Pharmaceuticals are one of the most important applications for 3D printing today. Pharmaceutical companies have been using the technology to create more effective drugs that are cheaper than traditional drugs. The process involves creating a three-dimensional model of a drug's molecular structure and then creating it in plastic or other materials by means of a 3D printer.
This process is much cheaper than what is spent on mass production and it also produces less waste as each dose is customised for you. The technology allows pharmacists to create individualised medications to suit their needs and requirements. When they create pills or tablets from plastic pellets or powders using standard manufacturing techniques such as injection moulding or extrusion processes, they are unable to do this and customisation is not possible without first changing their chemical composition.
In summary
3D printing technology has changed the way patients are treated. With this technology, doctors can better diagnose and treat patients with personalised medical models of their body parts and organs. 3D printing also makes it possible to create surgical guides for use during surgery and medical implants that are perfectly matched to the patient's anatomy. The possibilities for the use of 3D printing in regenerative medicine are also endless.