August 21, 2022 - Researchers at Carnegie Mellon University (CMU) have developed a method for3D printing tiny artistic ice structures. According to an article published on the university's official website, this high-speed, reproducible manufacturing method will "revolutionise" 3D printing technology in the future. Meanwhile, the technology could be widely used in the future for advanced manufacturing and biomedical engineering.
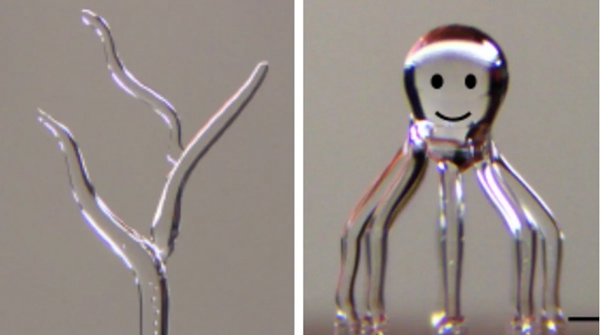
3D printing technique used to create complex ice structures
Using our ice 3D printing process, we can create microscopic ice templates with smooth walls and smooth transitional branching structures, which could be used in the future to make microscopic parts with well-defined internal voids," said Akash Garg, co-author of the study and a PhD scholar in mechanical engineering at the University.
Technical background
Garg collaborated with Saigopalakrishna Yerneni, a postdoctoral associate in chemical engineering at CMU, on this research.
Water is considered the best choice for bioengineering applications as it is the most abundant substance on the earth's surface and the main building block of all living organisms. The simple and rapid phase change process of ice formation from water makes it a very environmentally friendly structural material.
Garg says: "There is no more biocompatible natural material than water."
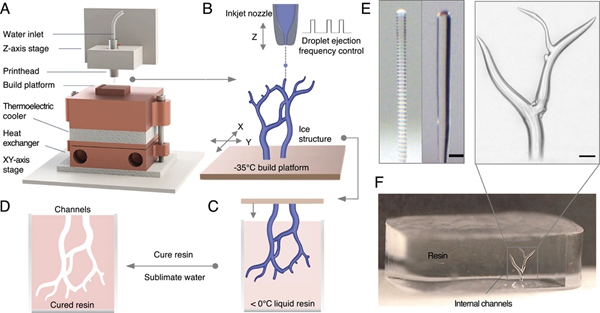
△ Freeform ice printing (3D-ICE). a) Customised 3D printing system and its main components, including cooling system, motion table, piezoelectric nozzles. b) Piezoelectric inkjet nozzles are used to eject water droplets (diameter = 50 microns) onto a cold build platform kept at -35°C. The planar (X-Y) movement of the build platform is synchronised with the water droplet discharge to print complex ice geometries
How does it work?
The printed ice structure is used as a 'reverse form' or ice template used as a sacrificial geometry and the ice structure is immersed in a cooled build material, such as resin in liquid or gel form.
After the material has set or cured, the water is removed. To this end, the ice can be melted to evacuate the water. Alternatively, ice can be sublimated by converting it into water vapour rather than liquid water. Because ice can be easily sublimated, it can be easily removed after casting and curing the surrounding structural material.
A high-resolution 3D printing system is used to deposit water droplets onto a temperature-controlled platform at -35 degrees Celsius, which rapidly converts the water into ice.
The new process enables printing with smooth surfaces and branching geometries with smooth transitions by regulating the jet frequency of the water droplets and synchronising them with the platform movement.
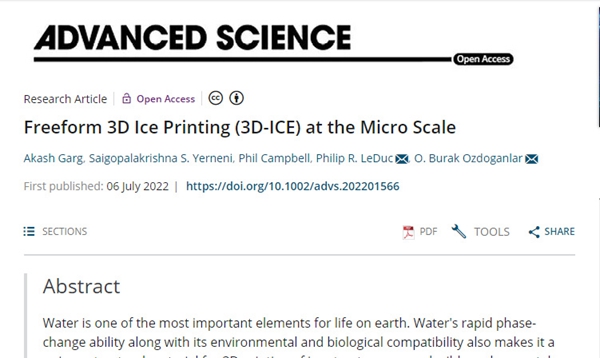
△For more information, the research has been published in Advanced Science
An amazing achievement
The researchers demonstrated this by printing a tree, a spiral around a pole and even a one-and-a-half metre tall octopus figurine out of ice. Thanks to the rapid phase change of water and the strength of ice, 3D printing allows for arbitrary ice structures without the need for time-consuming layer-by-layer printing or support structures.
Garg explains that experiments were conducted to determine the print path, speed of motion and droplet frequency required to create light-skating ice structures with straight, angled, branching and layered geometries in a reproducible manner.
Burak Ozdoganlar, associate director overseeing the research CMU's Engineering Research Accelerator, explained: "This is an amazing achievement that will lead to exciting scientific advances."
He continues, "We believe this approach has enormous potential to revolutionise tissue engineering and other fields that require microstructures with complex channels, such as microfluidics and soft robotics."
The team claims that within just one year the ice 3D process could be used for engineering applications such as creating pneumatic channels for soft robots. However, clinical applications of tissue engineering will take much longer. In the future, this new process approach, could also open up new opportunities for microfluidics, biomedical devices, flexible electronics and art.