Introduction: Hypersonic speed is a popular area of research, with the hope that vehicles can be developed that travel several times faster than sound. In order to reach speeds in excess of Mach 5, metals need to constantly break through the high temperatures of extreme environments. Already, a growing number of hypersonic researchers, have turned to experimenting with3D printing to develop super parts using the technology's unique materials and techniques.
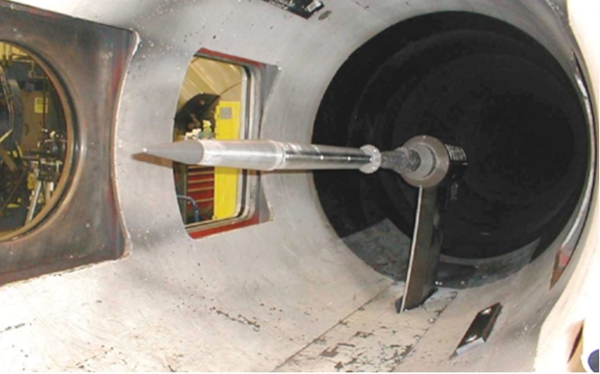
△ The US Air Force's White Oak 9 hypervelocity wind tunnel, testing the Terminal High Altitude Area Defence (THAAD) missile
19 August 2022 - The US Air Force is testing the role of 3D printing in an ultra-high-speed wind tunnel at the Arnold Engineering Development Center in White Oak, Maryland, Antarctic Bear has learned.
Early 3D printing research in the hypervelocity wind tunnel
The wind tunnel is being used by the US Air Force for validation of hypersonic ground tests and computational simulations. The facility team initially purchased a desktop material extruder seven years ago, but was unable to produce anything substantial. in 2019, Samuel Gigioli, a wind tunnel systems and nitrogen supply engineer at No. 9, set out to restart the 3D printing project. This time the engineers, used the technology to print tools such as plastic mounting jigs, fixtures, gauges and others.
Terminal High Altitude Area Defence (THAAD) missiles are designed to intercept and destroy ballistic missiles in and out of the atmosphere while they are in the final stages of flight. The THAAD missile shown here is in AEDC's Hypervelocity Wind Tunnel Facility #9 in White Oak, Maryland, to gather highly accurate static stability and drag data. Once proven, the same test models and instrumentation will be used at the Von Karman Gas Dynamics Facility to confirm that complementary testing capabilities exist between the two AEDC facilities.
As a result, they have purchased two additional 3D printers, including a vat photopolymeriser for detailed parts, and a large filament extruder. With in-house 3D printing, the team was able to obtain parts in just a few hours rather than weeks, Gigioli says: "There have been a number of prototype 3D printing tools applied to wind tunnel testing. In fact, a very critical aerospace optics part was made using our resin 3D printer, along with a number of printers making measurement or other miscellaneous parts."
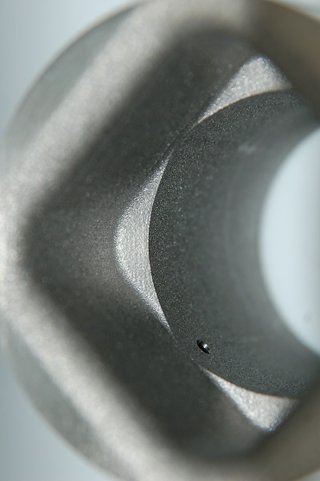
△ Close up of 3D printed high temperature resistant metal liner
Ultra-high speed wind tunnel using high temperature resistant metal 3D printed liners
In February 2019, the team undertook more advanced 3D printing research, using laser powder bed fusion technology to open a high-temperature resistant metal 3D printing hardware project for Wind Tunnel 9 production. The aim is to reduce the lead time and cost of high-temperature parts used in the tunnel.
Gigioli said: "The parts in Wind Tunnel 9, are continuously exposed to very high pressures and temperatures, and the lifespan of these parts is significantly shorter than those inside other wind tunnels. Now, using 3D printing technology, these parts can withstand temperatures of up to 3,000 degrees Fahrenheit (1,648° Fahrenheit). This is why the technology makes metals that deform relatively little in extreme heat environments."
Gigioli leads the team, managing materials, equipment and printers, while working alongside Nicholas Fredrick, Chief Facilities Engineer for Wind Tunnel 9. One contractor prints the parts and manages the production workflow, while the other provides the printing powder and performs material characterisation.
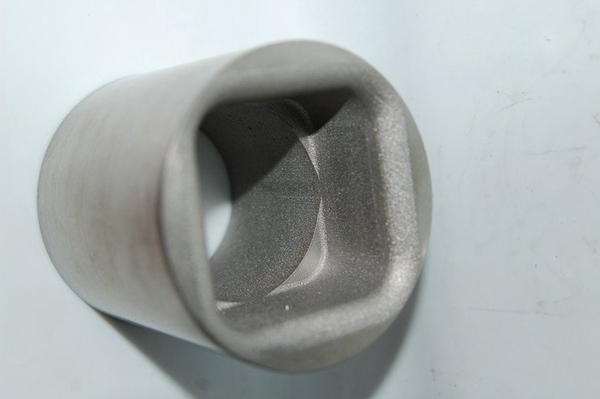
The Δ hypervelocity wind tunnel uses a high temperature resistant metal liner manufactured by 3D printing. It is one of the components that safeguard the wind tunnel under high Mach operation, and it can withstand temperatures of several thousand degrees. The outer diameter is approximately 3 inches, the inner diameter is approximately 2 inches and the length is 3 inches
Among the parts printed by the team, this metal 3D printed high temperature resistant liner is a key structural component for the stable operation of the hypervelocity wind tunnel. The part was placed between two blast diaphragms in wind tunnel 9 and is part of a component that operates as a high-speed valve in the tunnel. According to Gigioli, the 3D printed liner performs better than its conventionally manufactured counterpart." Gigioli said, "The part is cheaper to manufacture, faster to manufacture and deliver, and more resilient to cyclic temperature loads, and the 3D printing process creates a very unique microstructure in the material, resulting in a part that has different structural and thermal properties than a traditional forged metal blank."
Next, the team will test a 3D printed particle separator for filtering particles from the air inside the tunnel, and once completed, the part will be tested in high Mach conditions around September. With advanced 3D printing technology advancing at a rapid pace, other global participants in the hypersonic arms race now include Purdue University, Astro America, Orbital ATK and Raytheon, as well as VELO3D, GE and Lockheed Martin.