British Formula One team McLaren, which now 3D prints up to 9,000 parts a year, used five Stratasys Neo 800 3D printersto create many of the aerodynamic parts in its front and rear wing development program, as well as large elements of the car's side body and top body. The technology is also advanced enough to be used in end-use applications while continuing to help accelerate its aerospace testing program, according to Tim Chapman, the team's AM lead.
"Wind tunnel testing remains the gold standard for assessing how each surface works together, both as an assembly and as a complete vehicle," explained Chapman. "Our Neo Series 3D printers have helped us dramatically reduce the lead time for aerodynamic wind tunnel components and projects. Stereolithography and materials have evolved - changing the way we use it. We are no longer just making prototypes."
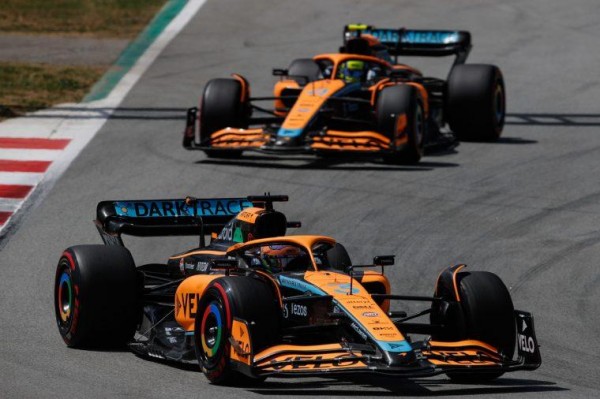
McLaren 2022 Formula 1 car. Photo from Stratasys.
Stratasys' SLA 3D printing expansion
Over the past 24 months, Stratasys has expanded its portfolio to include more technologies and extended its reach beyond users of its proprietary fused deposition modeling (FDM) system. To date, in addition to the Xaar 3D acquisition, Stratasys has also acquired EnvisionTEC to build its digital light projection (DLP) offering, which heralds the launch of its H-Series 3D printers.
In February 2021, Stratasys also acquired SLA 3D printing company RPS, a move that combines its acquired Neo series of industrial stereolithography machines into its broader offering. As a result, Stratasys' SLA product line now includes the Neo 450s, Neo 450e and Neo 800 3D printers, the latter with a build volume of 800 x 800 x 600 mm and lasers that can focus to 150-600 micron sizes.
While the acquisition resulted in the scrapping of Stratasys' V650 SLA 3D printer, it provided the company with access to RPS' already established customer base, thus strengthening its position in the automotive and tooling markets. At the time, Stratasys CEO Yoav Zeif also praised the Neo's "reliable and accurate build" as "superior" to the competition's, and it seems to be playing out now at McLaren.
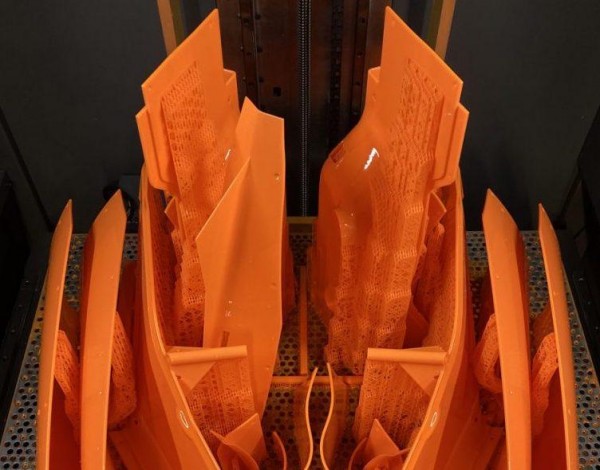
A set of Stratasys Neo 800-3D printed aerospace parts. Photo from Stratasys.
McLaren's aerodynamic advances
McLaren's partnership with Stratasys dates back to at least 2017, when they agreed to an initial four-year collaboration, and since then the British company has continued to make progress on its in-house 3D printed fleet. Installed at the team's Woking site, its system allows 3D printing of jigs, templates and small molds that would otherwise be machined in a slower, more material-intensive process.
However, McLaren primarily uses its Neo 800 to support its wind tunnel testing program, deploying them to 3D print 60 percent scale models of the intended parts. In turn, these were developed iteratively to optimize the team's aero kit and find more downforce for its current car and effectively provide it with more grip and balance its front and rear loads.
In doing so, Stratasys says its partners now report "significant progress" in its wind tunnel testing program, particularly due to the accuracy and throughput of the Neo 800. The machine's large bed allows for the generation of 50 to 60 air pressure housings designed to embed parts in McLaren race cars and enable its pit walls to monitor the aerodynamic performance of their cars.
Stratasys' 3D printer also allowed the company to produce large parts, such as scale model top bodies, in as little as three days while reducing its associated costs by not having to outsource them to a contractor. McLaren saved further time by using Somos PerFORM Reflect, a resin with a 30 percent reduction in post-processing time, which Chapman said sped up the entire testing process. "We found that the HD components of our Neo machine required minimal manual finishing, which allowed for faster passage through the wind tunnel," Chapman added. "In addition to speed, we can now produce wind tunnel parts with the highest precision, detail and surface finish, which allows our team to enhance testing and find innovative new ideas to improve performance."
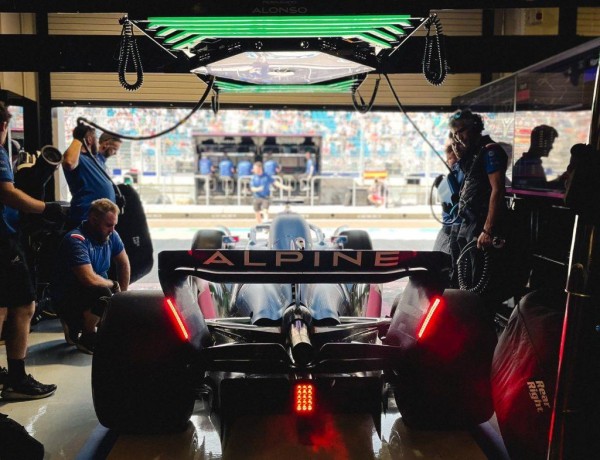
Additive Manufacturing in Formula 1
Stratasys' 3D printers are far from the only printers used in the world of Formula 1, and the technology continues to be deployed on a large scale in the production of wind tunnel test parts. In fact, Alpine's Pat Warner revealed the extent of 3D printing in F1 when he spoke to the 3D printing industry in May, with SLA being used extensively for aerodynamic prototyping.
Williams Racing, for example, partnered with Nexa3D last season to create functional components using the company's high-speed NXE400 3D printer. Specifically, Williams used the technology to 3D print F1 wind tunnel test parts as a means to evaluate the aerodynamics of its cars and remain competitive.
On the metal 3D printing front, the Alfa Romeo ORLEN F1 team also continues to deploy Additive Industries' technology in the production of its cars. While the team's latest challenger has fewer additive manufactured aerospace parts than before, it is still said to feature several 3D printed F1-class "key components.