The IMDEA Materials Institute in Madrid is developing new embedded sensors that can monitor aircraft in flight in real time. In order to achieve optimal performance and perform the best functions, the researchers have chosen 3D printing technology for its manufacture. Thanks to the uniqueness of this technology, humans can achieve safer flight because the 3D printed sensors have better predictability as well as maintenance, with the ability to notify maintenance personnel of problems before a devastating crash occurs.
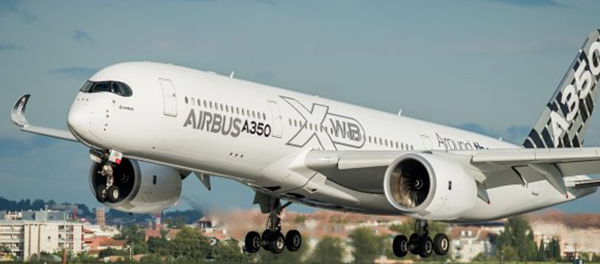
3D printed aircraft sensors
The work, called the "Digital Methods for Improved Manufacturing of Next Generation Multifunctional Airframe Parts (DOMMINIO)" project and funded by the Horizon 2020 research program, saw the IMDEA team 3D print parts with embedded carbon nanotube fibers. The piezoresistive properties of carbon nanotubes can be used to generate relevant data and for monitoring the parts.
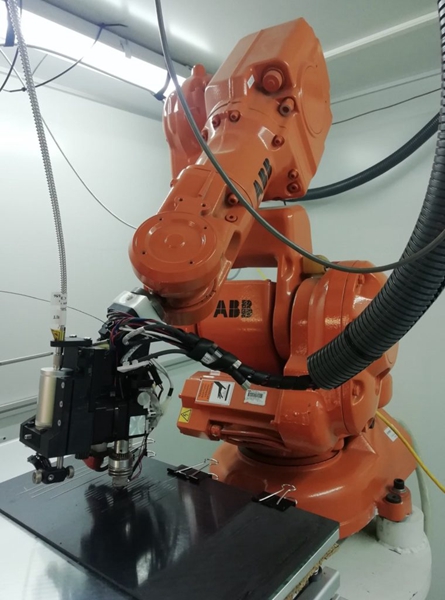
Additive manufacturing (AM) can reduce assembly costs while reducing the amount of wires needed to connect sensors together. There are statistically 70 to 300 miles of wires in aircraft, and approximately 100 to 400 wire harnesses are needed to hold sensors in place, so reducing wire connections is necessary and economical. 3D printed sensors are also light and consume relatively little energy.
IMDEA materials researcher Moisés Zarzoso notes, "Fibers were chosen for the sensor materials, which are very light and consume very little energy compared to existing materials. They are also 3D printable and easily embedded in parts made from conventional carbon fibers, bearing in mind that carbon fibers are a very common material in aircraft production."
From sensors to digital twins
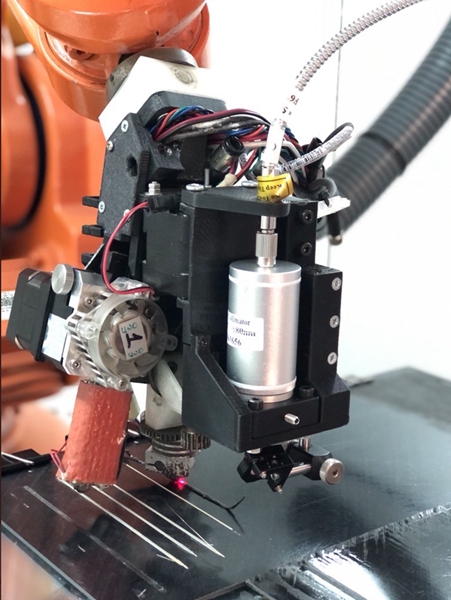
Key to the project was the creation of an aircraft simulation model using digital twins (which are simulation processes that leverage data from physical models, sensor updates, and operational histories to integrate multi-disciplinary, multi-physical quantities, multi-scales, and multi-probabilities, complete with mapping in virtual space to reflect the full life-cycle processes of the corresponding physical equipment).IMDEA is a leader in this field, using information from embedded sensors IMDEA is a leader in this field, using information collected from embedded sensors to create digital twins of physical components.
They are called digital twins because they are very accurate digital models that are updated throughout the life cycle, replicating the physical parts or components within the aircraft in real time," explains Zarzoso. Through their embedded sensors, the physical parts are able to communicate directly with engineers on the ground. For example, if you are affected by hail during a flight, the sensor records information related to possible damage to the part, which is then automatically sent to its digital twin. Using this information, the simulations we are developing will be able to analyze the risk that potential impacts could lead to the structural integrity of the component and determine its remaining life."
Improving Aircraft Maintenance with 3D Printed Smart Sensors
With this technology, airlines can not only fly safer, but also save money in a variety of ways, including: more accurate maintenance intervals, signaling problems before they cause flight delays, and monitoring and analysis of components. Real-time monitoring can look at sensor-driven aircraft maintenance in a whole new way, rather than the schedule-driven approach used today.
Event-based signals could become an important part of airframe and aircraft component monitoring. Researchers could develop protocols to look for telltale signs of impending failures or to conduct specific monitoring in the face of different events. Knowledge of in-flight failures may even allow crews to pre-empt landing aircraft, thereby shortening flights that could crash hours later due to critical component failures.
Many components on aircraft are now 3D printed composites. Embedding carbon nanotubes while using robotic arms to manufacture components seems to fit well into the overall workflow. For metallic materials, sensors can be integrated using ultrasonic AM technology like Fabrisonic's, which uses no heat during the printing of the object, ensuring successful sensor manufacturing. Many nanoprinting companies can also offer 3D printed sensor components for strain, vibration, pressure or more.
What is clear is that embedded sensors make sense for high-value and critical objects or processes, such as dams or aircraft. For these types of objects, 3D printing can provide a cost effective way to fabricate integrated sensor packages and embed them into our world.