After the 3D printing job is completed, the part itself usually needs to be processed for post-processing
After the3D printing job is complete, the part itself usually needs to be post-processed. Post-processing refers to all the work performed on the part after it comes out of the 3D printer, including but not limited to cleaning, surface preparation, annealing and even coloring.
Post-processing techniques in 3D printing are as diverse as the manufacturing process itself, and each has its own specific requirements. Post-processing is also a key step in the 3D printing process, and today this article gives you an introduction to cleaning, annealing, and coloring.
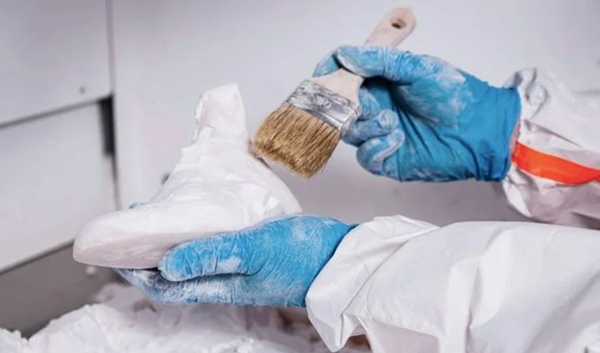
Post-processing in 3D printing is mainly used to improve the aesthetics of the manufactured part and its performance. For example, making the surface smoother or annealing the component to increase its strength and change its electrical conductivity. While some post-processing techniques are also available for 3D printing processes, most post-processing techniques are based on other manufacturing methods than additive manufacturing. Post-processing techniques in additive manufacturing processes can be somewhat different, for example, FDM parts must be treated differently than metal parts. Therefore, post-processing is an important aspect of the 3D printing process to consider.
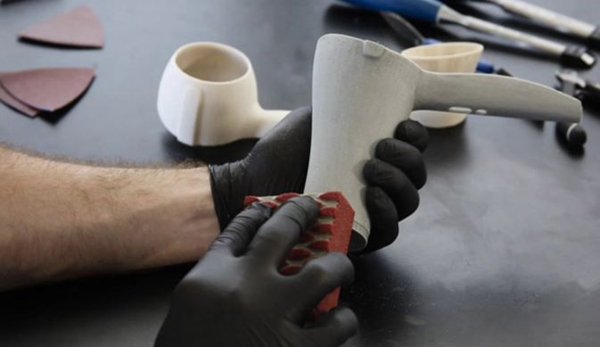
△ Post-processing is used to improve the aesthetics of 3D printed parts (photo credit: Sinterit)
Introduction to post-processing methods
● First is the cleaning of the parts. Part cleaning includes many things, such as desoldering, rinsing, brushing, blowing, etc. The goal is to remove any excess powder or resin material. Depending on the printing process used, this step will take varying amounts of time. For example, with powder sintering, this is usually a very time consuming step that increases manufacturing time.
● The second category is annealing. This step focuses on increasing the temperature of the part to improve its mechanical properties. These mechanical properties include heat resistance, UV resistance, and even its strength or thermal stability. This step mainly involves polymer parts - for example, for resin processes, there are "curing" machines designed directly for a particular printer. For powder bonding or indirect metal 3D printing processes, the part must be degreased and then sintered in a suitable oven. Therefore, annealing techniques are often used to improve the final performance and functionality of the part.
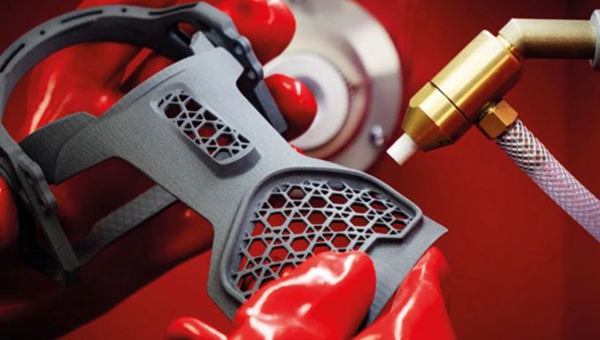
△ Image credit: MakerBot
● There are two classes of operations that can be used to optimize the appearance of a part: surface treatment and coloring.
The former includes all methods used to improve appearance: smoothing, polishing, sandblasting, penetrating, or milling. There are many processes available to refine the surface of a part by adding or removing material. For example, sanding removes surface unevenness, while spraying adds a layer of material for a better shine.
Coloring is primarily referred to as staining and painting. The choice between the two depends largely on the printing material used. For example, staining is more suitable for polymer powder-based processes, while painting is more suitable for parts made with FDM.
Benefits and limitations of post-processing
● Post-processing in 3D printing is a key step in improving the visual appearance of a part and its final characteristics. Thanks to different technologies, 3D printed parts can reach their full potential and can even be marketed as end-use parts.
Post-processing allows the user to correct certain print defects that can be "camouflaged" by removing the appearance of the printed layers. In addition, some plastic parts have similar properties to metal parts due to post-processing, resulting in a significant price reduction.
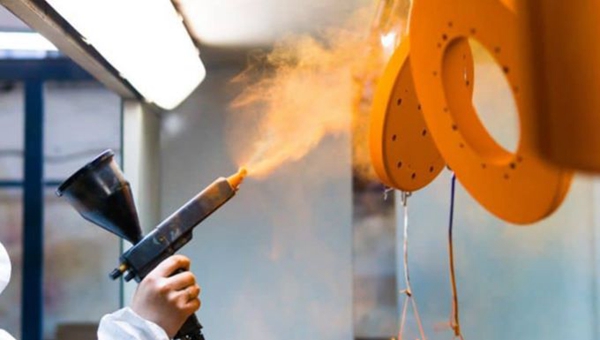
△ coloring technology (photo credit: BigRep)
Of course, post-processing has challenges and limitations that the market has been trying to address for years. one of the biggest obstacles to 3D printing post-processing is the time it takes. According to an annual study published by PostProcess Technologies, 53 percent of participants said their biggest challenge was the amount of time post-processing takes to work. These steps are still too time-consuming and do not meet the goal of reducing manufacturing time with 3D printing. As a result, automated processes have become the choice of many professionals in the field. These automated steps reduce labor and ensure employee safety.