Russian scientists 3D-printed miniature permanent magnets
Scientists from the Ural Federal University and the Ural Branch of the Russian Academy of Sciences are jointly working on a project to determine the optimal conditions for 3D printing permanent magnets from hard magnetic compounds of rare earth metals.
Scientists from the Ural Federal University and the Ural Branch of the Russian Academy of Sciences are jointly working on a project to determine the optimal conditions for 3D printing permanent magnets from hard magnetic compounds of rare earth metals.
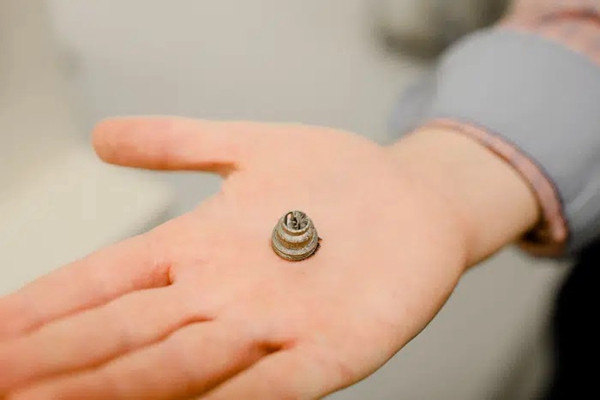
Permanent magnets can maintain a magnetic field source over a long period of time and are used in a wide variety of industries and devices, such as the manufacture of modern electric motors, household appliances, and computer equipment, among many other appliances. Permanent magnets manufactured by conventional methods are difficult to achieve tiny size and usually have two magnetic poles, one in the north and one in the south.
From a technical point of view, manufacturing complex and small permanent magnets is not an easy task. 3D printing technology, on the other hand, can be used to make complex-shaped permanent magnets. After several experiments, Ural scientists have managed to determine the optimal parameters for 3D printing permanent magnets using selective laser sintering and magnetic powders.
Moreover, 3D printing can also change the internal properties of magnets at the production stage. For example, changing the chemical composition of the compound, the degree of spatial orientation and crystallographic texture of the crystals, as well as affecting the coercivity (resistance to demagnetization).
"When small permanent magnets were originally manufactured, they were typically machined and milled in large pieces, and about half of them would become industrial waste. 3D printing, on the other hand, avoids this situation and creates complex permanent magnets, such as one with five south poles and five north poles, a configuration necessary for pacemakers. Currently, the electric motor rotors of pacemakers are assembled under a microscope, using separate permanent magnets." explains researcher Dmitry Neznakhin.
They have now 3D printed permanent magnets that are only 1 mm thick, using a base material that is a powder containing samarium, zirconium, iron and titanium.
"We found that adding a fusible powder of samarium, copper and cobalt alloy when sintering the sample preserves the magnetic characteristics of the main magnetic powder." Neznagin added, "The melting temperature of this alloy is lower than the change in the properties of the main alloy, which is why the final material retains its coercive force and density."