Australian additive manufacturing company AML3D (ASX: AL3) will use its patented wire-arc additive manufacturing (WAM) technology to 3D metal print prototype parts for nine Hunter-class frigates built and designed by defense contractor BAE Systems for the Royal Australian Navy
Recently, Australian additive manufacturing company AML3D (ASX: AL3) will use its patented wire-arc additive manufacturing (WAM) technology to 3D metal print prototype parts for nine Hunter-class frigates built and designed by defense contractor BAE Systems for the Royal Australian Navy, Mohou.com has learned. As part of the deal, AML3D will investigate the feasibility of manufacturing parts for the warfighter and deliver actual prototypes by the last quarter of 2022 as an alternative to future traditional casting projects.
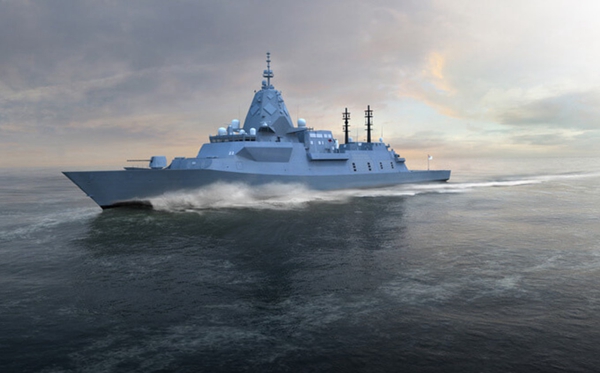
3D Printing for Australian Navy Projects
AML3D is one of 1,400 Australian companies pre-qualified in BAE Systems' Hunter-class (frigate) supply chain. Thanks to this multi-million dollar initiative, the Hunter Class Frigate Program (HCFP), the Australian Defence Force will have one of the highest levels of anti-submarine capability. They will replace its decades-old Anzac-class defense warships.
Created in 2015, the program is expected to launch the first-class HMAS (Queen's Australian Ship) Flinders by 2031 and will ensure that Australia has one of the most advanced ASW ships in the world. Given the increasingly tense military situation in the Asia-Pacific region, Australia believes it needs to be more ambitious in terms of undersea warfare, and the Hunter-class frigates that will help in the 2030s will boost its naval capabilities.
The two companies will become even closer partners following this recently announced deal. For BAE Systems, the new contract takes the HCFP program out of the validation testing phase. At the same time, AML3D will benefit from establishing yet another significant commercial relationship with BAE Systems, particularly in terms of the scale of its broader shipbuilding program.
In addition, the procurement contract for the Hunter-class prototype parts follows the commercial validation testing program launched in October 2020, demonstrating that AML3D's WAM technology is a cost-effective manufacturing solution with the potential to minimize lead times and meet BAE Systems' internal standards for additive manufacturing part production in Australia. In addition, the validation test results illustrate how WAM technology can support the ongoing naval shipbuilding and sustainment of sovereign capabilities as defined in the Australian government's naval shipbuilding program, which provides for the delivery of up to 21 Pacific patrol boats, 12 offshore patrol boats, 9 frigates and 12 future submarines.
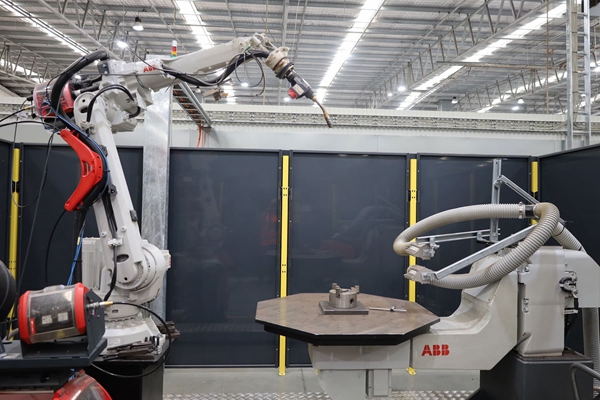
△ AML3D's WAM process. Image courtesy of AML3D.
AML3D's 3D printing track record
As the first large-scale 3D metal printing company in the world to be recognized by the maritime classification society Lloyd's Register, and certified by DNV, the world's leading maritime and industrial classification society for additive manufacturing, AML3D is a pioneer in providing certified high-strength parts for the maritime industry. This status makes the startup an attractive local high-tech manufacturing partner for BAE Systems, but not a new one. 2021, AML3D has revealed plans to build an R&D facility at a state-of-the-art future facility currently being developed by Flinders University and BAE Systems in Adelaide's Tonsley Innovation Precinct. In turn, the new site will further help the additive manufacturing equipment manufacturer develop its large-scale metal 3D printing capabilities.
This and other collaborative projects with BAE Systems expand on the extensive work AML3D is already doing in the defence sector, including a procurement contract with a new defence aerospace customer for a 500kg four-piece aluminium nozzle set; an agreement with Boeing to test aluminium parts for prototype components and a partnership with Austal to develop parts for maritime defence applications.
Commenting on the company's latest news, Ryan Millar, AML3D's recently appointed CEO, said, "Developing commercial relationships in the maritime and defense sectors is critical to AML3D's strategic growth plans. We are very confident that WAM® can meet BAE Systems' testing protocols and are pleased to have successfully taken this project out of the validation testing phase. The provision of prototype components to support BAE Systems' contract with the Royal Australian Navy for the construction of the Hunter-class frigate is another step in building a commercial relationship of great significance. particularly on the scale of BAE Systems Australia's broader shipbuilding program in Australia."
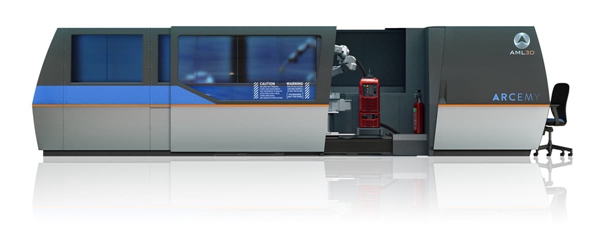
△ AML3D's Arcemy Large-Scale 3D Metal Printer AML3D's Arcemy Large-Scale 3D Metal Printer. Image courtesy of AML3D.
Currently valued at A$15.24 million (US$9.9 million), AML3D continues to realize its multi-phased growth strategy built on acquiring near-, medium- and long-term value drivers. With recent contract wins and ongoing contract negotiations with Tier 1 companies such as BAE, Thales, RheinMetall and Northrop Grumman, the Adelaide-based business is rapidly becoming a recognized supplier of 3D printed parts to major Australian companies.
With fast lead times based on its advanced WAM technology, it is becoming known for providing design optimization, short lead times and delivery times. In the short term, in addition to the industry certifications and standards already in place, AML3D is focusing on obtaining AS9100D certification, a measure that specifies additional requirements for the aerospace, space and defense industries, enhancing its prospects in these key market segments.