Six future trends in 3D printing
3D printing is becoming a widely used manufacturing technology, not only for prototypes, but also for small and medium-sized series. A compilation of six trends that will have a significant impact on the 3D printing industry and those who use 3D printing technology. Let's explore where the future of 3D printinglies, shall we?
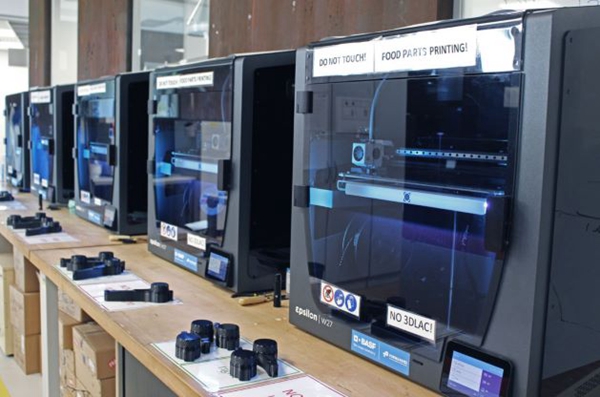
1. The New Era: Bigger, Faster, More Economical
3D printing/additive manufacturing (AM) technologies are evolving rapidly, and they are becoming bigger, faster, and more economical. The current growing demand for specialty materials in the 3D printing industry to meet the performance requirements needed for end-use parts will continue to drive the range and type of materials used. Key to next-generation printers, especially industrial-grade solutions, is their ability to handle a wider range of advanced materials, which opens the door for companies to benefit from AM, and while machine costs are still high, increased print speeds are lowering the price of parts. As more and more companies turn to 3D printing, it is believed that costs will become lower as well. The versatility of 3D printing is growing as processes such as dual extrusion are developed and we see more and more industries adopting 3D printing. Another trend is printing without the use of support structures, which again expands the range of applications AM can offer, and the potential for cost and time savings from unsupported printing is significant.
2. Improved efficiency and interoperability
To maximize the benefits of AM as an integrated supply chain approach, manufacturers need not only a large number of printers, but also materials and connections to other industry professionals. In order to maximize the potential of 3D printing, interoperability between different systems is becoming increasingly important. Automation and integrated availability of production and post-processing will continue to be an important trend in the coming years. am can provide a new approach to the supply chain where individual steps need to be integrated into one process, including conceptual design, materials, digital inventory, production and delivery. Providing a fully automated and secure platform will drive this change as manufacturers move into the Industry 4.0 era.
3. Develop common standards and synergies
From individual partnerships to entire work systems, increased collaboration can create mutual benefits and synergies that result in better products for the end customer. The main driving factor in wanting to expand production in the 3D printing industry is collaboration. More and more manufacturers are seeing the need for more comprehensive collaboration. the 3D printing field must work together to set standards, printers and post-processing systems should be able to work together, and the production data collected can improve printers and materials. Close collaboration is the key to achieving the best solutions. There is an urgent need for a system that connects global service providers, material producers and printers, knowing that only by working closely together and communicating permanently will manufacturers be able to provide the best solutions for their customers.
4. Safety and quality assurance
For industrial production, companies must ensure that their 3D printed parts meet the necessary quality requirements. In addition, data ownership has an important role and data management will be a huge concern in the future. In terms of quality assurance, production partners need to be carefully selected, their capabilities examined, and repeatable fit-for-purpose parts ensured. Of course this is far from enough and further steps need to be taken to ensure that design data is in the hands of the company. The company fixes the manufacturing parameters that can be performed by encrypting the data, so that parts can only be produced in the required quantities and materials. By collecting manufacturing data and analyzing it, errors can be quickly identified and processes can be improved to ensure that all quality requirements are met.
5. Create a resilient supply chain
Issues such as the new crown pneumonia and cross-border trade disputes have demonstrated the fragility of supply chains. 3D printing has been used to solve these problems in the past and its use will continue to grow. With decentralized supply chains and on-demand production near consumer locations, 3D printing makes supply chains shorter, stronger, and more resilient. Physical inventory is the weak link in any supply chain, and parts can be stored digitally rather than in a physical warehouse, which eliminates storage and transportation costs. With a digital warehouse, once a part is ordered, it can be automatically sent to the most appropriate and suitable production partner based on location, capacity and capability. Parts can be produced anywhere, anytime and increase supply chain resiliency.
6. Drive sustainability
3D can reduce waste in the production process. By designing parts specifically for 3D printing, the weight of the final part can be significantly reduced, thereby reducing the amount of material required for production. In addition, as mentioned earlier, when 3D printing is used as part of an on-demand, decentralized digital warehouse, it can reduce the number of parts in inventory and associated waste, as well as CO₂ emissions during transportation. Looking ahead, the use of 3D printing is expected to increase as part of the company's sustainability strategy. To further improve the sustainability of the technology, it is necessary to reduce the energy consumption in the production process, and we are already seeing huge improvements in this area. In addition, we will see an increase in sustainable 3D printing materials such as recycled, reusable and biodegradable plastics.