Austrian 3D printing company Cubicure has introduced a new 3D printing system that enables an industrial-volume stereolithography production process
Cubicure, an Austrian 3D printing company, has introduced a new 3D printing system that enables an industrial batch stereolithography production process. Recently, Mohou.com learned that they have now developed a new clean solution for post-processing polymer components for additive manufacturing that can further improve material sustainability as well as save significant time and money in post-processing. cubicure says that depending on the process chain, this solution can be optimized individually.
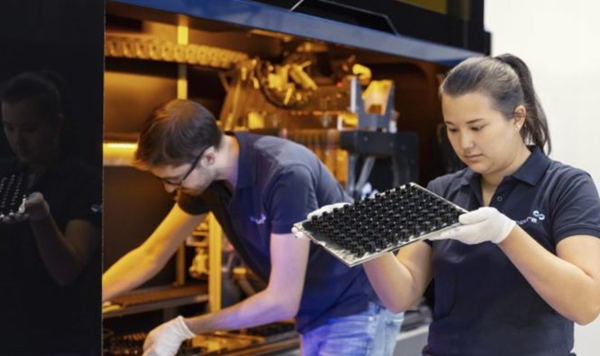
Cubicure GmbH develops, produces and distributes industrial 3D printing solutions for polymer parts. With a focus on academia and an ambition to help shape the digital future of manufacturing, the Vienna-based company has been showing the way to rapid production since 2015. Their thermal lithography process enables the additive manufacturing of elastic, high-precision parts like never before. Now they're back with a post-processing solution for light-based 3D printing Customizable cleaning solutions require industrial-grade improvements in the post-processing of 3D printed polymer parts, with millions of high-precision parts printed and cleaned each year.
● The first cleaning stage is the removal of material residue from the printing platform. This residual resin is collected in a container and recycled for use through the 3D printing process," explains Dr. Bernhard Busetti, product manager for Cubicure 3D printing systems, "Thermolithography is already a highly material-efficient process. With our post-processing solution, the removal of excess material during component cleaning can simply be reused, which makes the company more sustainable and saves costs."
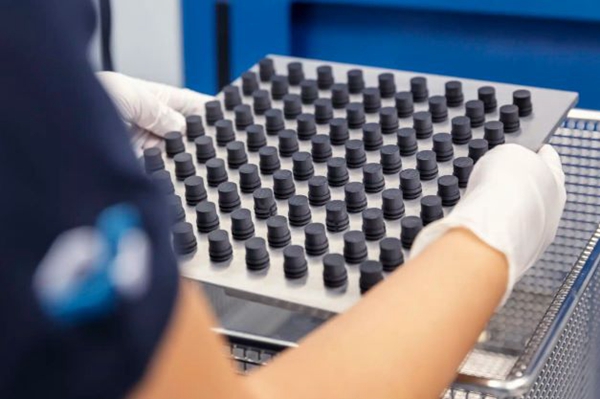
△Cubicure demonstrates industrial polymer reprocessing. A customizable cleaning solution that recycles residual resin.
● The additively manufactured components are then processed in an energy-efficient cleaning facility. The equipment is equipped with an ultrasonic device that gently cleans precision components. The cleaning agent is recovered through a built-in distillation unit, so that very little new solvent needs to be added, even at very high production volumes. Users can also use superheated steam for fine cleaning.
Finally, the components are dried in a vacuum cycle. The use of the cleaning system increases machine safety as cleaning is fully automated and takes place in a closed area. Depending on the application, the printed components can be separated directly after printing, between cleaning steps or at the end of the entire process chain.
Cubicure's cleaning solution represents a further step on the road to fully digital production. The development of a method for sustainable cleaning of polymer components provides a future-proof solution for integrating additive manufacturing into modern industrial production processes.