3D printed wearable connected medical devices
Introduction: The powerful convergence of data, healthcare, software, private enterprise and personalised healthcare devices is set to be a highly dynamic area. Imagine your smartphone or other device only being interconnected and communicating with your fitness app, your doctor, your insurance company, your health and your assessment of your own health, so you can get up-to-date information on your pulse, your walking steps, your sleep time and more, keeping an eye on your body! Now that this connected device has evolved, some in the media believe it complements this customisation with3D printing technology!
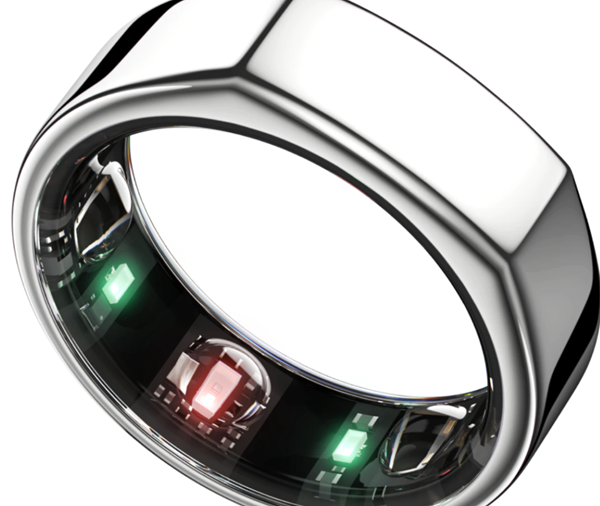
Connected medical devices
It is not yet clear what the main users who can access this health data will be. Will you share your health data with Apple, Google, your insurance company? Can your doctor download the data so they can view it? Or will the data sensors we carry with us on a daily basis exist as a fully parallel system? Will you be able to share it with your personal trainer? Or will we all share it with our friends? Or would we consider it a very personal thing? The above questions are still unknown, and while the scope of use of these connected devices is unclear in terms of some laws and rules, what is known is this: the wearables market is valued at $115.8B in 2021 and could grow to $380.5B by 2028. the fitness tracker market is worth a whopping $34B per year. In terms of devices, in addition to the leading US companies, Chinese giants such as Samsung, Oppo and Xiaomi are among them, selling tracking devices priced from $19 to $400. There are also products such as the Oura Ring, various sleep trackers, Whitings' ECG tracker and other wearable biosensors.
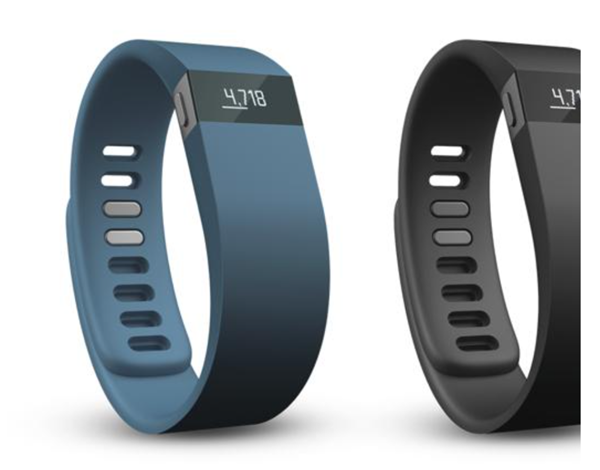
The potential for these devices is huge. Obesity rates in OECD countries range from 4% to 40%. 70% of Americans believe they don't sleep well one day a month, while 11% say they never sleep well. 60% of American adults don't exercise enough. This could be significantly reduced with the right incentives, such as apps, sensors and mobile phones. What's more, in an increasingly busy world, we can find certainty about our health and our own rhythm through daily step counts or related programs.
Now imagine how software can study human health by monitoring millions of people and how the effects of exercise or diet can be more accurately tested by tracking a million apps. The information would be more recent and the size of the cohort would be larger than almost any study to date. If apps can transmit the latest algorithms and amazing AI content and combine it with cutting-edge tested health advice to deliver better results for millions of people. This is a very large business and has a major impact on global health. With over 6.4 billion people owning a mobile phone, this is a globally shared industry that can become part of most people's lives.
The health, daily life, longevity and financial implications could be enormous. With such large numbers and huge impacts, 3D printing's role in connected healthcare devices need only be small to be extremely valuable. Currently, 3D printing is already being used in orthopaedics, surgical guides, medical models and bioprinting. However, connected medical devices remain a neglected application of 3D printing.
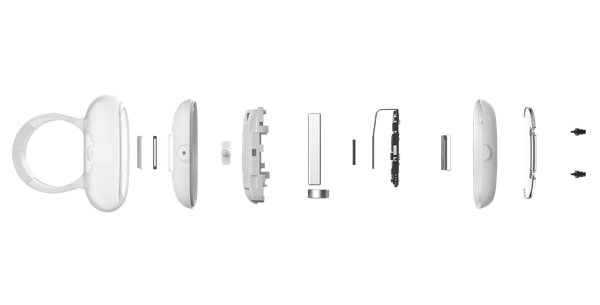
● Prototyping
The field of prototyping of connected devices is still an untapped 'zone'. There are known to be 500 startups in the fitness band alone, and at least 64 IoT healthcare monitoring companies. This is a great opportunity for OEMs and service providers who have not yet addressed it.
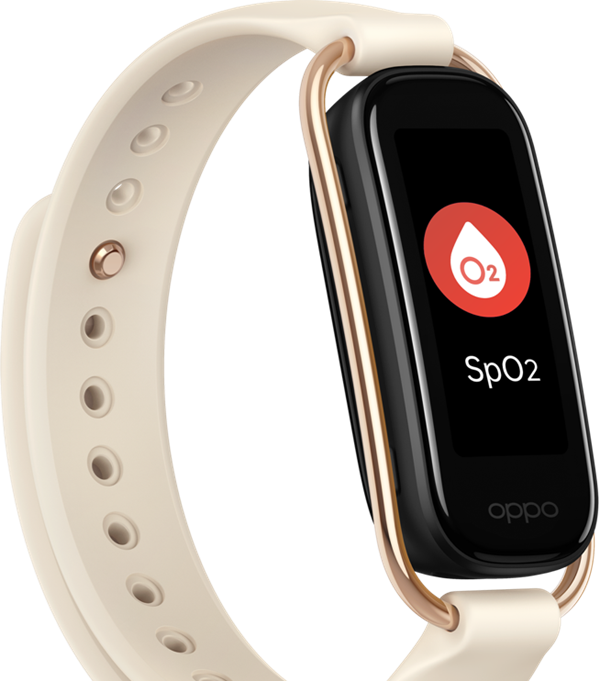
● Small size
Often we compare additive manufacturing to mass manufacturing, especially injection moulding. For start-ups, however, we can not only reduce the limitations of traditional production by making individual and batch prototypes, but also small final part series. This can be done by individual 3D printing or by using 3D printed moulds. Startups are able to produce series of 50 to 500 devices at a relatively cheap price, allowing them to get to market faster or test with many customers to improve the suitability and functionality of their products.
● Multiple sizes
These connected devices often benefit from body conformability. This means that they will have a curved shape, which makes them more complex and expensive to produce. What's more, these curves will be more comfortable if they are available in a variety of sizes. With 3D printing, we can produce more curved surfaces directly or indirectly through moulding as needed to meet the various size variations of the user.
● 3D printed electronics
Conformal and bending devices will also pose no small challenge for components such as antennas and batteries. Using additive manufacturing, we can 3D print conformal batteries and antennas while extending their functionality. Antennas can be bent to follow the shape of the wrist and avoid the microprocessor, while also having holes for use as fasteners. Overall, this would enable more form factors and reduce the size of components. Similarly, 3D printed sensors themselves could play a role in making these devices lighter and more practical. Aerosol injection for mass manufacturing of 3D printed antennas has been proven and can be industrialised.
● Mass reduction
In general, we can use 3D printing to reduce the mass of components in order to make these devices conformable, smaller, lighter or less conspicuous. This is a decisive advantage for these products, especially fitness bracelets, as they need to be worn during strenuous exercise or throughout the day.
● Reduced supply chain risk
Additive manufacturing makes increasing sense when we consider the extended and fragile supply chain and the vulnerability of tools, end-use parts and mould components. Companies may give up profits to reduce dependence on suppliers or speed up market entry, even though components printed in 3D will be more expensive.
● Mass customisation
As very personal and fashionable items, these devices would be ideal for mass customisation. Mass customisation and 3D printing can work well together, allowing customers to design their own unique devices that they love and match their lifestyles.
All in all, we believe that 3D printing technology has great potential for connected healthcare devices!