Recently, outdoor equipment manufacturer Jack Wolfskin, has improved the durability, breathability and greatly reduced dead weight of its mountain backpacks through 3D printing technology, Mohou.com has learned. "Comfort, weight control and ventilation are always core issues in sports backpack design, says Magdalen Hamel, Wolfskin equipment category manager. "Our new backpack with 3D printing technology will benefit hikers and take the industry in a new direction.
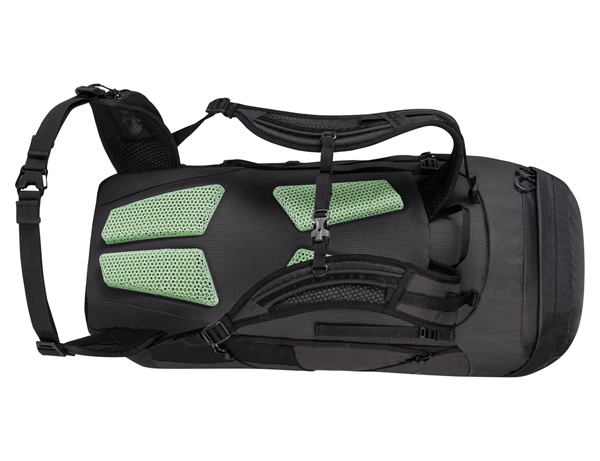
△3D printed 3D Aerorise hiking backpack
3D Aerorise hiking backpack
Now, Wolf Claw has also developed its own 3D printed backpack using additive manufacturing technology. The company has partnered with plastics technology company OECHSLER and 3D printer manufacturer Carbon to develop the 3D Aerorise hiking backpack. It is all about using the technology to reduce waste, improve customisation and offer a range of design benefits.
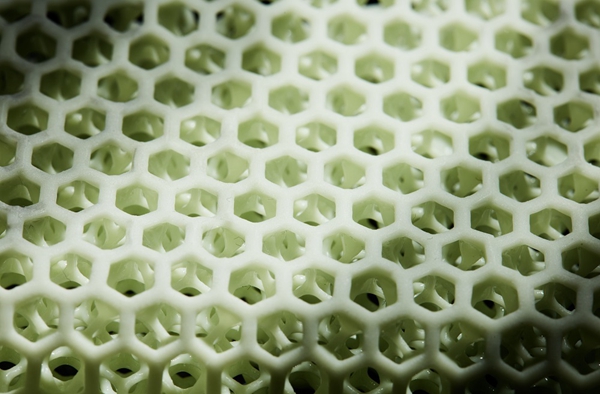
△Better rear ventilation thanks to a 3D printed lattice structure with thousands of pillars
The backpack is made up of four 3D printed panels on the shoulders and lower back. The focus is on the design solution of the panels, currently only possible through 3D printing technology, which are made of an open structure with thousands of pillars, while the lattice pattern provides vertical and horizontal robustness for comfort and load distribution. At the same time, four separate 3D printed panels provide a lightweight, multi-zone body fit with good ventilation, capable of reducing back temperatures by up to 5°C.
As 3D printing allows for a multi-zone fit, the system is designed to eliminate common pain points of hiking backpacks such as weight, durability and ventilation. the body of the Aerorise backpack is made from 100% recycled 70D polyamide and has a maximum load carrying capacity of 40 litres. "3D printed manufacturing is changing the world of outdoor equipment and sporting goods," says Matthias Weisskopf, Managing Director of Jückeschler. "The collaboration with Wolf Claw has enabled us to further develop the Aerorise mountaineering backpack and together we can solve the technical problems that have always existed in the industry.
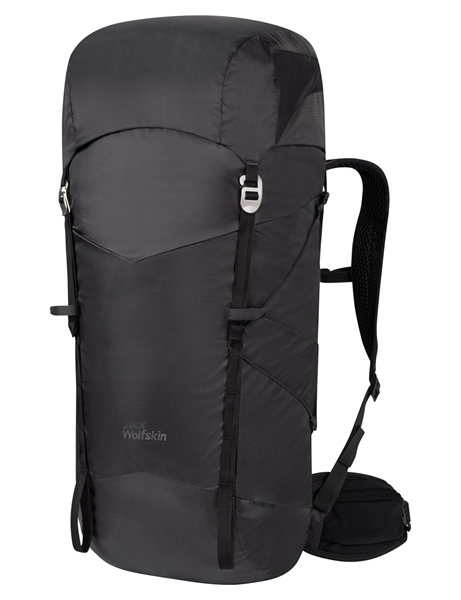
The △Aerorise range of packs will offer the wearer better weight, durability and breathability
Opening up a new trend in 3D printing with AERORISE
Wolfpaw claims that this new 3D printed range is just the beginning and that it will continue to upgrade existing products with this technology in the future. Meanwhile, the already launched 3D Aerorise backpack, which is expected to debut in spring 2023, will be available in three models: 3D Aerorise 40L, 20L and 30L. In the future, once the brand officially brings the range to market, it will definitely transition to other sports lines, such as sneakers, after gaining some market feedback. "Carbon's 3D printing technology, software and advanced materials accelerate the time it takes for a product to go from idea, to mass market," said Andreas Tulaj, Carbon's Vice President of European Sales. "Using Carbon's Idea-to-Production platform, Wolf Claw improved the performance of the 3D Aerorise backpack and worked with Yukschler to develop components that were not possible with traditional manufacturing processes, while, at the same time, bringing it to market quickly."
3D printed performance equipment
3D printing technology, thanks to its ability to provide greater customisation in the production process, enhanced designs and reduced material waste and lead times, is increasingly being used in the performance sports sector.
3D printing and scanning technology, for example, has created custom aerodynamic tights for Olympic cyclists, developed more ergonomic grips for the Korean archery team and helped the Chinese speed skating team win two gold medals at the 2022 Winter Olympics in Beijing.
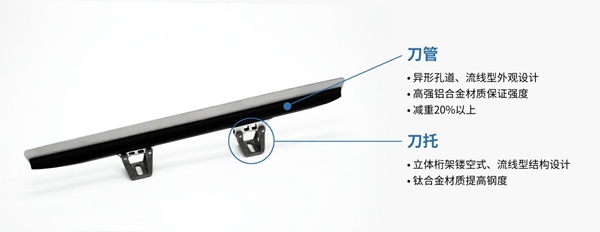
△Short track speed skating ice skates prepared using metal 3D printing technology, weighing more than 20% less than traditional ice skates
The Winter Olympics will use metal 3D printing technology to provide equipment optimisation solutions for the Chinese short track speed skating team, tailoring new lightweight, personalised short track speed skating skates for athletes. The new 3D-printed ice skates have a streamlined body structure, with a reasonable structure and low wind resistance. In addition, while traditional ice skates are made from aluminium alloy, the 3D printed ice skates are made from aluminium-magnesium-scandium alloy. The aluminium-magnesium-scandium alloy is a new generation of aerospace structural materials based on traditional aluminium-magnesium alloys. Structural parts printed with this material have a higher strength than traditional aluminium alloys and can replace some titanium alloy components to achieve weight and cost reductions.
Another notable application of 3D printing in performance sports is the 4DFWD performance running shoe jointly developed by Adidas and Carbon, which was officially launched last year and is being worn by several athletes at the 2022 Tokyo Olympics.