Casting is a basic industrial industry with an irreplaceable position. There are currently about 26,000 foundries in China and the annual production of castings accounts for about half of the total global production. Among the many casting methods, sand casting is the most common production method, and the products produced through sand casting account for more than 90% of the total number of castings. However, in the traditional sand casting method, the following problems exist.
A● high labour intensity, poor working environment, and widespread shortage of staff, difficulty in recruiting and retaining staff.
B● high mould-making costs and long lead times, making it difficult to meet the demand for multi-variety, small-lot production
C● low density and precision when manufacturing moulds with complex geometry, increasing the difficulty of subsequent processing.
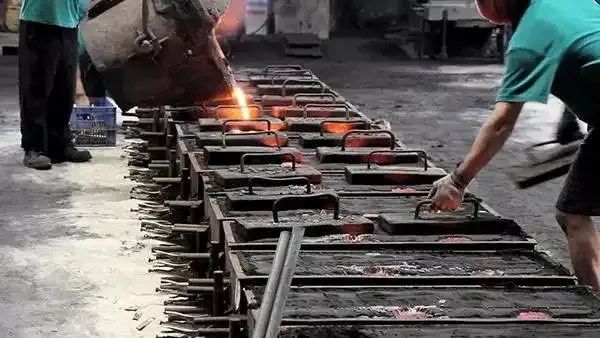
Additive manufacturing technology (3D printing) breaks the shackles of traditional preparation processes. With the aid of computer-aided design, the 3D model of a part is divided into multiple 2D sections using the discrete/stacking principle based on a digital model, and the sections are stacked into 3D entities by way of superposition. This technology is currently being applied in the field of sand casting, catering to the needs of the industry by.
A● Instead of manual operations, all moulding processes are carried out in a relatively closed box, with no dust raised during the printing process, substantially improving the working environment and reducing heavy physical labour.
B●Omitting the process of making moulds, which not only saves production costs but also enhances the speed and flexibility of product trial production.
C● Improving the dimensional accuracy of products, enhancing the control of sand size, reducing the enterprises' reliance on highly skilled workers, enhancing product quality, not only reducing the subsequent product scrap rate due to dimensional problems, but also improving the efficiency of subsequent casting product processing.
As the fields of aviation, aerospace, shipping and new energy vehicles continue to develop in the direction of high performance, high reliability and low cost, more and more parts and components tend to be high strength, lightweight and complex, thus promoting the application of additive manufacturing technology in many fields.
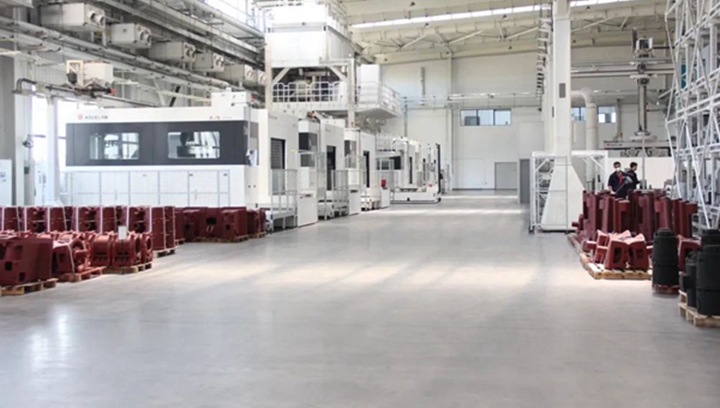
Relying on Share Group's more than 50 years of foundry experience, Share Intelligent Equipment Co., Ltd. began to focus on the industrial application research of foundry 3D printing in 2012. Up to now, it has independently developed more than ten types of foundry sand 3D printing equipment and established five foundry 3D printing intelligent demonstration factories across the country. Since its industrial production ten years ago, it has served customers in the fields of military industry, aerospace, engines, robots and compressors.
The following together to understand the typical application cases of various industries that have shared services.
1 Engine flywheel casing
Product weight: 50-100kg
Difficulty: The main structure is a large plane with thin walls (7mm), with a large local thickness, prone to defects such as bubbles and cold compartments
Solution: Inclined pouring process, multi-point exhaust in large plane to ensure good filling
3D printing delivery time: 15 days
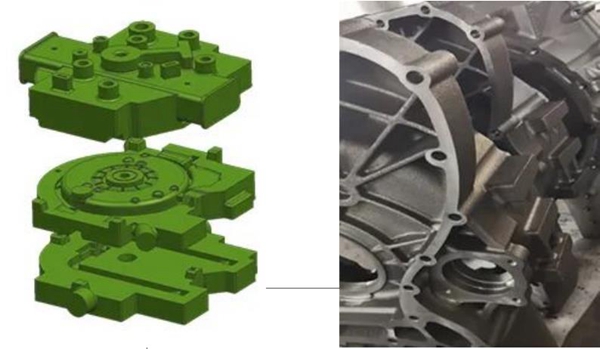
2 Screw compressor casing
Product weight: approx. 1 tonne
Product difficulty: complex internal cavity structure; thick local structure, easy to shrink loose; many processing drilling parts
Solution: isolate thick parts and use strong cooling measures; use special melting process (CE4.4 ~ 4.5, △ T ≤ 3) to achieve simultaneous solidification
Moulding cost: 700,000 RMB for wooden moulds
Mould start-up period: 50 days
3D printing lead time: 25 days
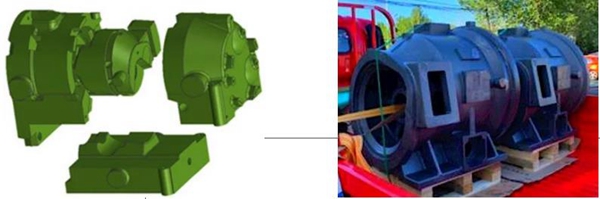
3 Multi-way valves
Product weight: 15-400kg
Product difficulty: high dimensional accuracy of the internal runner, and can not appear phi seam and other defects; body sampling (near the heart) for metallurgical testing, requiring a spheroidization rate of ≥ 90%, the number of graphite spheres ≥ 100
Solution: The runner core is made into a whole core to ensure dimensional accuracy and avoid defects such as phi seams in the core; long-lasting inoculant and special spheroidizing agent are used to achieve the metallographic requirements
Moulding cost: 500,000 RMB for metal moulds
Mould start-up period: 90 days
3D printing delivery cycle: 15 days
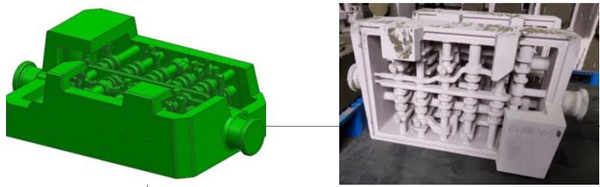
4 Internal combustion engine
Product weight: 30-2000kg
Product difficulty: the product structure is particularly complex, does not allow any form of welding and patching, high cost and difficulty to open the mould, sand core size is large
Solution: 3D printing is used for the overall modelling of double-layer tubes, cavity cores and complex internal cavity structures. The most complex products only need to be divided into 5 sand cores
Cost saving: 20%-60% of the mould cost
Mould start-up cycle: 3-6 months
3D printing lead time: 25-30 days for first part delivery
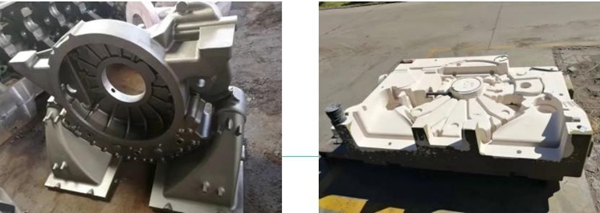
5 Aluminium alloy casting
Product weight: 2-60kg
Product Difficulty: High dimensional accuracy of internal runners, and no defects such as phi seams; complex structure, difficult mould forming
Solution: Simplify the process by joining multiple cores into one, reducing the number of cores, ensuring dimensional accuracy and avoiding defects such as core pockets
Cost saving: 20%-60% of mould cost
Mould start-up cycle: 20-90 days
3D printing delivery cycle: 15-25 days delivery
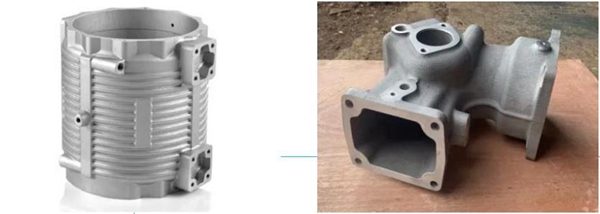
The integration of 3D printing technology with traditional industries has become an inevitable trend. In the field of sand casting, 3D printing technology has also opened up new avenues for the development and production of rapid, green, multi-functional, large, complex and demanding parts. Sharing will continue to focus on promoting the industrial application of casting 3D printing technology to help transform and upgrade the foundry industry.