3D printing can drive advanced healthcare by providing cost-effective and easy-to-use medical devices.
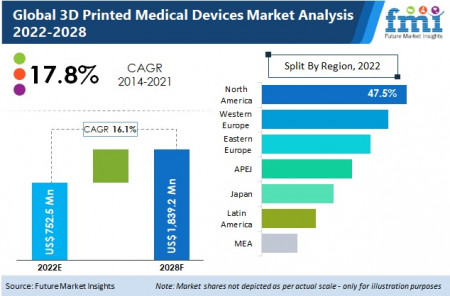
Before we talk about the healthcare sector, we can talk about the electronics sector. In electronics, 3D inkjet printers are used to print circuits using an ink that is a conductive material that can print circuits not only on flat 2D surfaces, but also on 3D products. Whereas traditional circuit board (PCB) production uses subtractive manufacturing methods, 3D printing is a form of additive manufacturing. The subtractive manufacturing process involves etching, drilling or cutting from a solid board to build the final product. It is ideal for applications that use a wide range of materials and for the manufacture of PCBs for large size products. Additive manufacturing is the process of adding layers of material and bonding these layers together to develop products. 3D printing requires the ability to control the density of the material and the ability to make complex features, making the manufacturing process versatile. It can be used in a range of engineering and manufacturing applications, particularly in custom manufacturing.
Advantages of 3D printing in medical device manufacturing
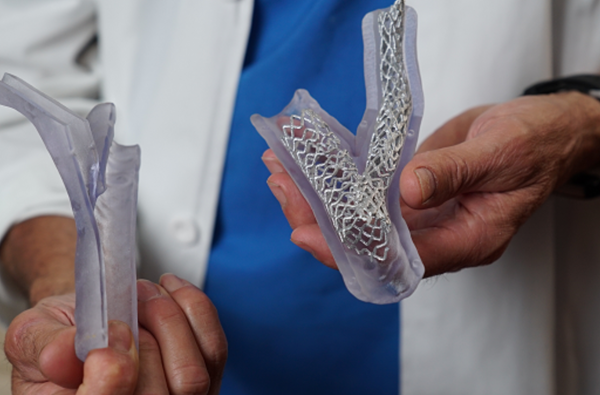
3D printing is very economical and provides rapid PCB prototyping without the need for complex manufacturing steps. It optimises the PCB design process by avoiding design errors that can occur during the initial PCB design phase. 3D printing on flexible PCBs is easy and allows for multi-layer PCB printing using the latest design software. As manufacturing trends grow and software improves, 3D printing will become more than just a prototyping tool and can be a viable alternative to producing parts. 3D printing is already being used to manufacture the final components of a wide range of medical devices such as hearing aids and dental implants, making it more beneficial for small production runs.
As the demand for miniature medical devices continues to grow, 3D printing has become the right choice for effective manufacturing. Biomedical sensors, medical implants and surgical aids are some of the key applications for 3D printed electronics in healthcare. Looking ahead, 3D printing can assist in the development of new treatment strategies by providing low-cost and personalised health services in the field of medicine.
3D printing technologies in medical device manufacturing
The most common 3D printing techniques used for plastic parts are stereolithography (SLA), selective laser sintering (SLS) and fused deposition moulding (FDM). If the device is manufactured using metal, direct metal laser sintering (DMLS) or laser melting (SLM) methods can be used. SLA technology is suitable for prototypes with tight tolerances and smooth surfaces, such as dental and medical end-use parts, while SLS is the best choice for complex geometries such as prosthetics. In applications using metals, FDM printing can be used for low-cost prototyping. DMLS or SLM printing is used to build robust and durable parts, such as orthopaedic implants.
Applications of 3D printing in medical devices
● Building rapid prototypes: Medical PCB prototyping is a critical process involving multiple iterations. 3D printing offers the flexibility to develop prototypes of complex circuits for medical devices. It allows rapid testing and verification of properties such as strength, functionality and heat resistance. 3D prototypes can be used as proofs of concept for new designs and as models for investor proposals. Thanks to 3D printing, it is now possible to build efficient and customised medical devices.
● Tissue engineering using biomaterials: regenerative medicine uses biomaterials, cells, etc. to create synthetic organs, blood vessels, bones, valves and even synthetic skin. 3D printing supports tissue engineering with the potential to replace human organ transplants. These developments will transform healthcare delivery in the coming years.
● Production of customised medicines: The introduction of 3D printing offers the pharmaceutical industry the opportunity to personalise the preparation of medicines. Doctors can provide more specific drugs based on a patient's age, weight and medical history. This can result in significant cost and resource savings. Bioprinted organs are used in medical clinical trials. This increases drug productivity and also reduces the adverse effects on animals that are often used for drug testing purposes.
● Less expensive prostheses and organ models: synthetic organs can be of great help in medical research and treatment planning. Organ models can be used to understand complex surgeries and give patients an idea of their health status. Prosthetics are expensive and not easily affordable for many patients. However, 3D printing can significantly reduce their cost.
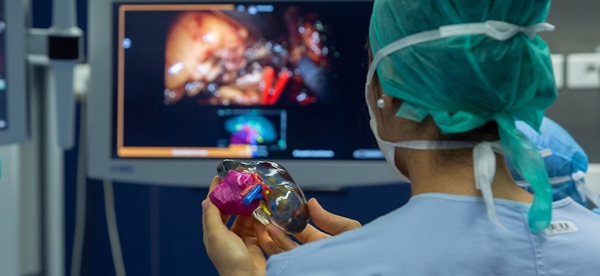
● Improving the lifestyles of older people: Chronic diseases have always posed a challenge to healthcare services. 3D printed orthopaedic implants, synthetic heart valves and bones have improved the overall quality of life for many patients.
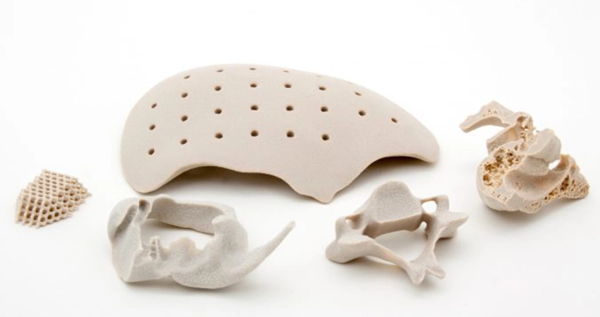
● Advanced healthcare services: 3D printing can provide biocompatible, personalised dressing materials. The flexibility of these materials promotes rapid wound healing. Surgical instruments developed using 3D printing have improved the accuracy of procedures. Microfluidic chips can now be manufactured using 3D printing technology. These chips can detect abnormalities in the body and can be used for real-time diagnosis.
Regulatory approval for 3D-printed medical devices
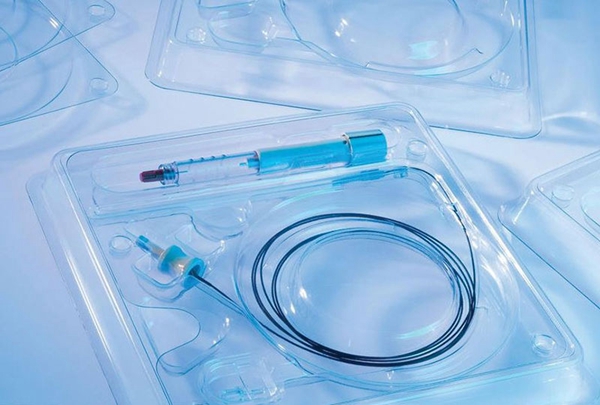
Manufacturing medical devices using 3D printing technology has become very easy. The flexibility to produce highly customised products has led to the widespread use of 3D printing in the production of medical devices. The advantages of 3D printing are complemented by the safety of medical devices. For this reason, regulatory approval for 3D printed medical devices is mandatory.
The US Food and Drug Administration (FDA) classifies medical devices into three categories based on the risks involved. Although the FDA does not regulate 3D printers, it does regulate medical devices manufactured using 3D printing. Regulatory review increases with the class of medical device.
Category 1 includes low-risk components such as bandages or handheld surgical instruments.
Category 2 includes moderate-risk devices such as syringes and blood transfusion kits.
Category 3 includes products used as life support systems. It can be pacemakers, defibrillators, ventilators or implanted prostheses. Detailed clinical trial data are required to ensure the safety of Class 3 medical devices.
Conclusion
Healthcare services can provide a high-quality patient experience through the use of medical devices based on 3D printing technology. There is huge scope for the medical and pharmaceutical sectors to take full advantage of the emerging 3D printing technologies.