Introduction: According to SmarTech Analysis' Market Opportunities for Additive Manufacturing in the General Industrial and Tooling Industries 2020-2029 (link to report at end of article), 3D printing for industrial manufacturing is expected to generate $5.48 billion in total revenue by 2029. One application that continues to receive attention is the additive manufacturing (AM) of cutting tools. So, what changes will 3D printing bring to the cutting tool sector?
一 3D printing makes large cutting tools more manageable
One of the drawbacks of manufacturing large parts, such as those for the automotive and aerospace industries, is that larger parts require larger cutting tools. However, as these tools are also heavy, there is a risk of damaging the spindle or the tool may fall off the machine during use.
At least one company has found a solution to this problem through 3D printing. Star SU Neher uses 3D printing technology to make cutting tools lighter, perform better and last longer than non-3D printed tools.
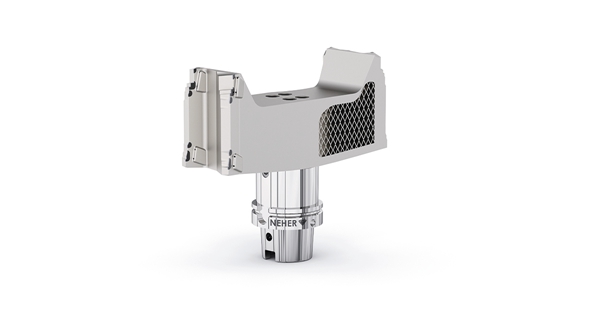
△ By designing the lattice structure, the weight of the tool can be reduced by as much as 30%. Image courtesy of Star SU Neher.
A tool designer at Star SU Neher mentioned that adding an internal lattice structure reduced the weight of their product by 30% without adversely affecting torsional strength. In addition, the company customises most of their cutting tools to meet the needs of individual components, and 3D printing helps to enable this flexibility.
One of the reasons why the company's 3D printed cutting tools last longer is the incorporation of cooling channels, a technology that is increasingly used in 3D printed cutting tools. Typically, such channels are created by drilling holes, however this method is limited in its effectiveness. With additive manufacturing, the channels can be designed directly into the part, increasing the overall efficiency of the tool. The increased coolant flow can result in a 30% increase in metal removal.
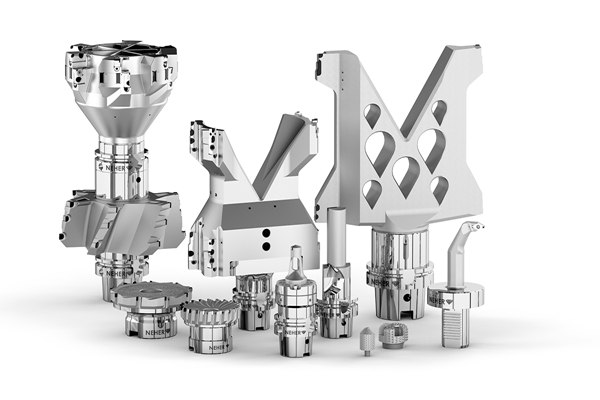
Δ3D printing makes it possible to reduce the weight of large cutting tool heads to limit damage or slippage variations in machine tool parts. Image credit: Star SU Neher.
Manufacturing large cutting tools by 3D printing is not necessarily faster than traditional manufacturing methods. It can still take up to 24 hours to produce a part that takes up the entire print bed at its size. However, given the other advantages, it often makes good business sense to pursue 3D printing.
二: 3D printing can promote better wear resistance
Cutting tool manufacturers working with customers in certain industries, such as the oil and gas and defence industries, often need to meet their needs for wear-resistant tools. Cutting tool manufacturer Kennametal specialises in products made from tungsten carbide. The company has an in-house product range made from WC material. Similar to the Star SU application, the printing process allows fluid cooling channels to be formed within the tool. Thanks to the design freedom of additive manufacturing, 3D printing allows for the manufacture of curved or bifurcated channels in a way that cannot be done with other manufacturing methods.
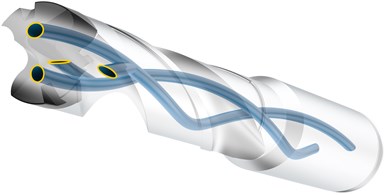
ΔKennametal is able to 3D print drill bodies with internal cooling channels. Image credit: Kennametal.
While Kennametal has both metal binder jetting and powder bed fusion (PBF) technologies, some cutting tools with diameters of 10mm or less will have to rely on powder bed fusion (PBF) technology. Manufacturers say that this gives them an economical way of producing tools and meeting customer demands. Weight reduction is also a possibility. In one example, a 3D-printed boring device for the production of electric vehicle parts is 15 to 20 pounds lighter than one made using conventional methods.
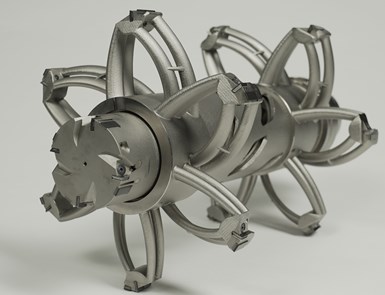
Δ3D printing has reduced the weight of this boring tool for manufacturing electric vehicle parts by 15 to 20 pounds. Photo courtesy of Kennametal.
三: 3D printing helps revolutionize cutting tools
The use of 3D printing to prepare cutting tools is not yet a widespread practice, but it is a technology worth exploring. For the time being, 3D printing is often cheaper and sometimes faster than traditional methods, depending on the object of application.
Additive manufacturing is not going to replace conventional methods of producing most cutting tools any time soon. Many of the efforts underway are still in the early stages of exploration, and manufacturers will certainly find situations where 3D printing is not suitable for producing specific cutting tool types.
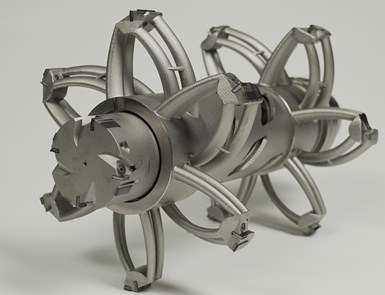
For tools with complex shapes, 3D printing is not a particularly good candidate. However, when the workpiece is a large part with a fairly regular geometry, it may make more sense to buy these off-the-shelf than to use a 3D printer to produce them.
Another thing to remember is that because 3D printing as a tool manufacturing method is a relatively new paradigm, decision makers may want to see how it pays off for similar companies before deciding whether to invest. Once they see the results, they may be more willing to scale up the process over time.
The relevant report is available at: https://www.smartechanalysis.com/reports/market-opportunities-for-additive-manufacturing-in-the-general-industry-and- tooling-sector-2020-2029/