PEUGEOT (France)'s new car, the 308, will feature special car parts made by 3D printing. The R&D team has started cooperation with HP Inc. and others to develop a new material Ultrasint (TPU) suitable for 3D printing, and the brand hopes to attract more customers through perfect design solutions.
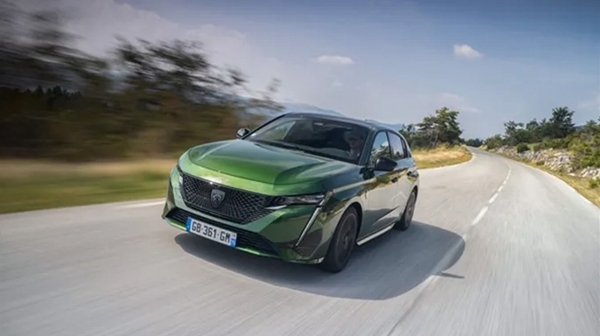
The △308 series is an upgraded version of the brand's 30008 SUV with a sporty look and plenty of storage space. Image from trendhunter
Redefining
Using 3D printing technology and new flexible polymers, the French manufacturer is redesigning automotive accessories. A wide selection of accessories will be available in the future PEUGEOT LIFESTYLE store, such as sunglasses holders, box holders and phone/card holders, all designed specifically for the new 308. This time, Peugeot's first foray into 3D printing technology for manufacturing car accessories is opening up a whole new door for the automotive industry.
Earlier, Peugeot's design, product, and R&D teams, in collaboration with HP Inc., Mäder and ERPRO, intended to take the design of cars to a whole new level. They used the industry's first 3D printing technology for the latest 308 model. The automotive parts were produced using a new 3D printer from HP Multi Jet Fusion (MJF). These accessories are designed to provide lightweight, durable and easy-to-use innovations that are changing the game for the industry.
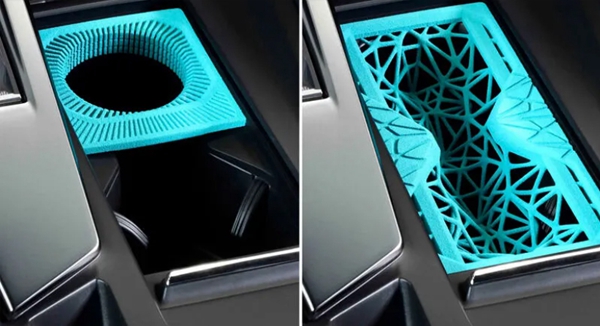
△ 3D printed parts can increase flexibility by addressing increasingly demanding and unpredictable market needs. Image from trendhunter
Flexible, Environmentally Friendly, Future Technology
By introducing advanced 3D printing technology to automotive parts, Peugeot is achieving a more environmentally friendly manufacturing concept. By saving resources and preventing waste through 3D printing technology, it is playing an important role in finding sustainable production solutions. Increasingly common, 3D printing is revolutionizing production processes in many industries, and with this new technology, flexibility can be increased by adapting to increasingly demanding and unpredictable market demands. A wide range of special items and accessories can be produced without the need for expensive molds and manufacturing tools.
Transition to industrial innovation
During the transition to automotive accessory technology, designers aimed to make accessories more eye-catching and attractive through the use of modern materials and innovations. The accessory solution was created after a detailed analysis of the customer's needs, and it has the following advantages.
1. 3D printing is constantly evolving in terms of materials used and production methods, and the technology offers additional cost advantages due to the decreasing production costs for companies;
2. Design freedom, with unlimited design potential due to the absence of injection molding and fewer production constraints and part complexity. At the same time 3D printing opens up new creative possibilities for designers.
3. optimized structures; lighter, more durable, fewer mounting parts, greater flexibility.
4. flexible production; shorter lead times due to custom production, thus eliminating the need for inventory and storage.
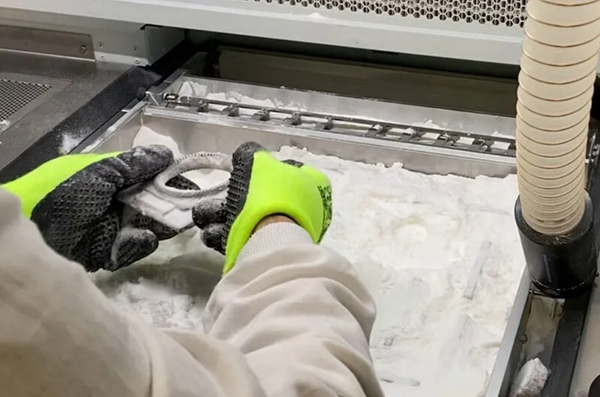
△Ultrasint thermoplastic polyurethane (TPU) flexible material is manufactured in collaboration with HP Inc. and BASF. Image from trendhunter
Because traditional materials do not achieve the desired results, the PEUGEOT Design "Color and Materials" team worked with project partners to develop Ultrasint, a more innovative-looking material using 3D printing technology.
1. Flexibility: a flexible, machinable and robust polymer.
2. speed: a very short production process that allows for mass production.
3. High quality: fine molecular characteristics for very fine detail presentation.
The flexible material, called Ultrasint thermoplastic polyurethane (TPU), is manufactured by HP Inc. in collaboration with BASF. They claim that this material is more durable, robust and flexible than traditional materials. It is suitable for applications such as shock-absorbing components and flexible webs that require high flexibility. The material can be used to produce parts with high surface quality and a very high level of detail.
In addition, the use of TPU technology in the interior of automobiles has gained a high level of interest from STELLANTIS, a leading global automotive manufacturer and travel service provider.