3D printing brings a new revolution in the manufacture of blades in terms of shaping and controllability.
Turbine engines, particularly gas or gas turbine engines, extract energy from the combustion gas stream through the engine's multiple rotating turbine blades, which are distributed in multiple turbine blade assemblies. While the blade body profiles are often designed as complex free-form surfaces for aerodynamic reasons and require the utmost precision in their manufacture, 3D printingbrings a new revolution in the manufacture of blades in terms of shaping and controllability.
Reducing the occurrence of cracks
Cracking is a fatal flaw in turbine engine blades during operation. The trend is towards more heat-resistant nickel-based alloys and increasingly complex cooling designs, with higher cooling requirements and efficient thermal insulation coatings. And 3D printing by achieving a more uniform and controllable crystal organization, more high temperature resistant composite materials, more complex cooling channels of the blade, and the metal matrix combined more closely with the thermal insulation coating, thus enhancing the performance of the blade, more effective to avoid the occurrence of cracks.
As the core component of an aerospace vehicle, the turbine blade, which determines the key performance of the engine, has become a top priority for research. The propulsive power of an aero-engine is closely related to the temperature of the turbine front inlet, and the temperature capacity of the turbine blades determines the propulsive power of the whole engine.
The hollow and cooling hole structure improves the cooling of the original turbine blade, this structure can effectively improve the turbine blade temperature capacity, and thus effectively increase the engine operating temperature, this more efficient air cooling method is the focus of current research. Improving the cooling capacity of turbine blades through complex air-cooled internal cavity structures has become the key to advanced engine manufacturing.
According to the Chinese Engineering Science1, the blade is structurally composed of three main parts: the blade body, the rim plate and the tenon. The blade body surface is the main body of the blade, its shape is usually designed to have high aerodynamic performance of the space free-form surface; mortise part is used to achieve the blade in the rotor disc fixed, also known as the blade root; edge plate for the blade body surface and the blade root mortise between the transition part. The blade transmits the force of the working medium on the blade body surface to the rotor spindle through the fit of the blade root tenon to the corresponding groove in the rotor disc, which in turn drives the external load to achieve power output.
Better cooling
GE's patent details how the nozzles that hold the blades and burner bushings around the engine burner can also be cooled better using cooling holes or serpentine circuits to avoid cracking.

© US11359494B2
The serpentine circuit may be a cooling aperture extending to any of a plurality of surfaces set along the blade, including at the tip, trailing edge and leading edge. The direction of the cooling flow at the leading edge then affects the durability of the turbine airfoil. The cooling fluid flow flows from the interior in a first direction through the curved channels of the cooling holes and out of the cooling holes. The cooling fluid flows converge in the first direction and simultaneously disperse in a second direction perpendicular to the first direction, both in a plane perpendicular to the flow direction, and finally discharge the cooling fluid close to the stagnation line of the engine components.
Better blades
Safer and more stable blades give GE's engines a competitive advantage. GE uses EBM 3D printing technology to manufacture turbine blades, using an electron beam as its energy source to melt metal powder layer by layer, made from the advanced aerospace material titanium aluminium (TiAl). This material is around 50% lighter than the nickel-based alloys commonly used for low-pressure turbine blades. Compared to its predecessor, the GE90 engine, this means a 10 per cent reduction in fuel consumption (and with it, emissions) and a weight reduction of around 200 kg for the GE9X.
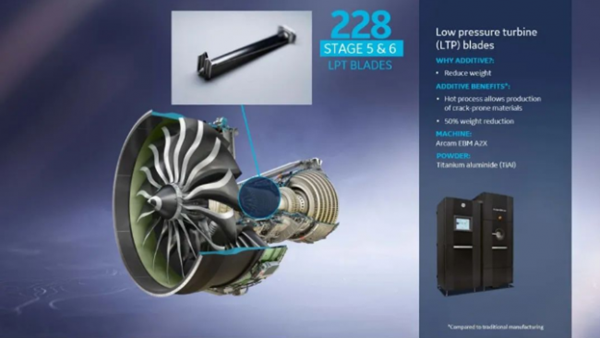
© GE
The GE9X engine, with its new materials, cooling technology and aerodynamic design, is the only engine option for the Boeing 777X family of aircraft, and is the culmination of General Motors' innovative research and development, with a 60:1 boost ratio that is the highest in the history of gas turbine aero engines. turbine blades, and is continually adding new equipment to increase production capacity for 3D printed blades. According to 3D Science Valley's market observation, GE covers a wide range of engine cooling patents, such as patents on air bearing cooling structures and thermal management methods for forked-finger turbine engines, patents on tilting burners for turbine engines, patents on fuel nozzles, patents on 3D printed fuel injectors and cooling systems l Patents for 3D printed integrated turbine covers with cooling channels, multi-layer outer wall turbine blade airfoils, etc.
l References.
1. China Engineering Science / Error analysis and compensation of composite blade profile measurement system