June 21 - Acoustics engineer Peter Riccardi has designed his own lab-grade microphone that can be 3D printed and assembled for less than $30.
June 21 - Acoustics engineer Peter Riccardi has designed his own lab-grade microphone that can be 3D printedand assembled for less than $30.
High-end lab-grade microphones are an essential tool for acousticians or acoustic engineers, providing the level of performance needed to capture precise physical signals during experiments. However, traditional condenser microphones from well-known manufacturers such as PCB Piezotronics sell for around $1000 reps. obtain."
Riccardi's homegrown device features a 3D printed housing and four internal MEMS microphones, designed to be an accessible alternative to those high-end systems. Despite costing just $30, the microphones are designed to provide similar background noise, frequency response, flatness and sensitivity in the 20Hz to 20kHz audio band.
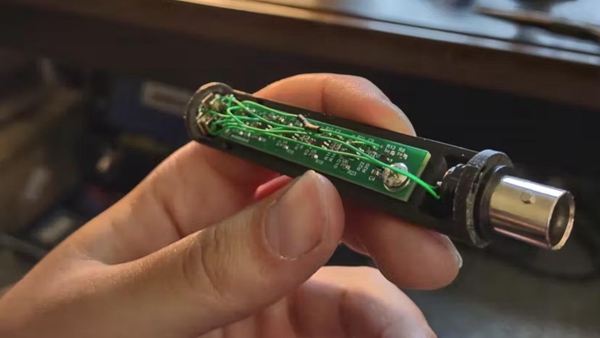
The total cost of the 3D printed microphone is less than US$30. Photo from Petri Caldi.
Designing and 3D printing a microphone
For his prototype, the engineer divided the electronics into two boards, the first of which is a MEMS carrier board. Four MEMS microphones are mounted on a circular PCB, which includes a series of small through-hole pads for all the required power and signal connections. The second board is the main board, which houses all the inputs and signal conditioning for the MEMS outputs.
The board then needs to be fixed to the mechanical assembly - this is where 3D printing comes in. Riccardi designed a simple cylindrical enclosure in SolidWorks and 3D printed the assembly in two parts using PLA. The shape and size of the enclosure is intended to mimic a commercially available microphone with a diameter of just 0.5 inches. Because the entire mechanical assembly is curved, it is very robust and can be tossed around without fear of damaging or breaking the housing," he adds. The opening in the MEMS carrier plate will need to be modified in the future, as there is very little material and stress concentration on the interlayer bonding. For now, it's working well."
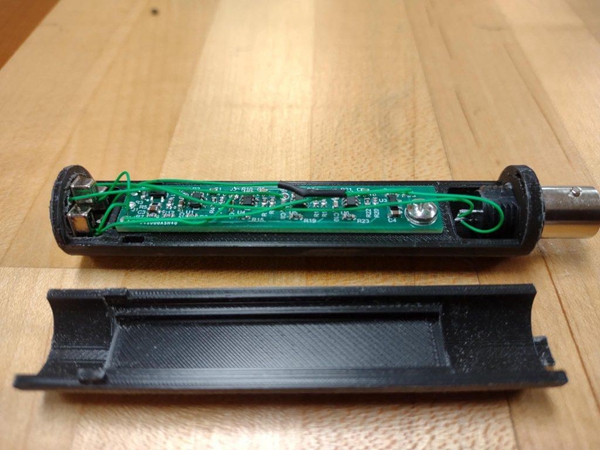
The 3D printed PLA housing is in two parts. Photo from Petri Caldi.
Does it perform better than commercial microphones?
The decision to use four MEMS microphones at once was well thought out. An electrical system with voltage drop components will inevitably generate electrical noise, which can corrupt signals and make them harder to read. This noise is random, but can be averaged to reduce its impact. By connecting four MEMS elements (noise sources) in parallel with small resistors, the output noise floor of the microphone can be reduced, thus easily improving the signal-to-noise ratio of the system. To test the performance of the 3D printed microphone, Riccardi completed tests in a semi-anechoic chamber (a very quiet room). He used an NI 4431 data acquisition system to compare the frequency response and noise measurements of the device with a PCB Piezotronics 378B20 free-field condenser microphone.
The results were impressive, to say the least. Riccardi's low-cost microphone has a sufficiently flat frequency response in the audio band, and its sensitivity proved to be high enough for practical measurements, albeit lower than the PCB product. However, below 200Hz, the 3D printed microphone actually performed slightly better than its commercial counterpart. Additional experiments are needed to more rigorously characterise the microphone," he writes. However, the initial results are very promising and the price makes it impossible to ignore."
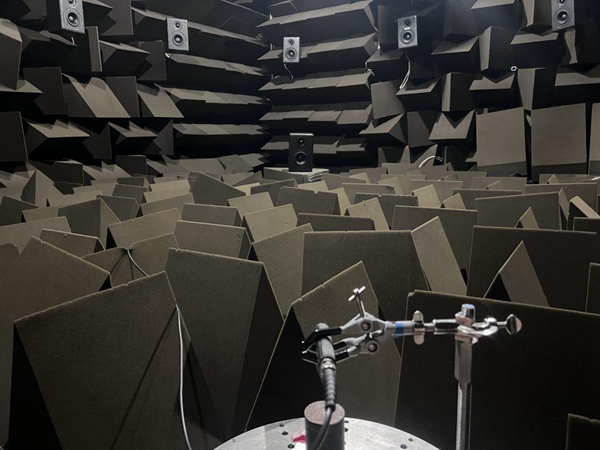
A 3D printed microphone being tested in a semi-anechoic chamber. Photo from Petri Caldi.
The rise of consumer-grade 3D printing technology has enabled creatives and hobbyists around the world to develop accessible versions of their products at relatively low cost. Earlier this year, hobbyist toy manufacturer Riskable developed an innovative key-switching mechanism for PC keyboards. The magnet-based design, called the 'Void Switch', is completely open source and can be manufactured at home using any common FFF 3D printer.
Elsewhere, YouTuber Akaki Kuumeri previously designed and 3D printed a novel joystick attachment for his Xbox Series X/S controller, turning it into a fully functional flight stick. More recently, he has gone on to build an open source library of 3D printable parts that attach to game controllers to enable non-standard hand positions, making it easier for people with physical disabilities to play video games.