Introduction, a few decades ago, one might not have thought that with the advent of CNC machines, the technology would replace traditional manual work methods. However, when new technologies emerge, there will always be sceptics, and at the same time there are those, who can capture the opportunity to stand out. Will 3D printing be next?
Evolve Additive Solutions says that wherever possible, the design benefits of 3D printing will come into play. The company has already started using 3D printing technology to produce polymer parts at high speeds.
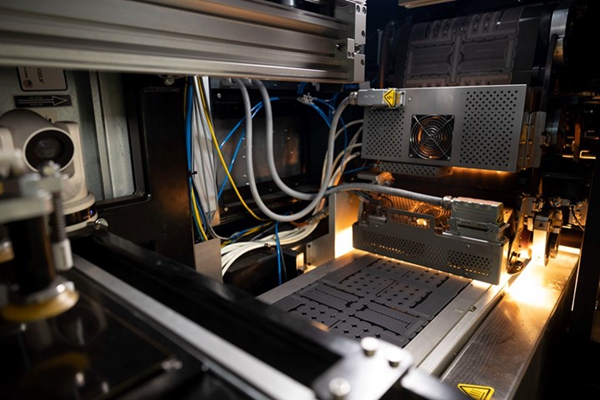
The ΔSTEP process, uses technology borrowed from high-speed imaging. It allows for batch printing of parts at deposition rates of up to 286 cubic inches per hour
The company is gearing up for 3D printing to be a direct replacement, in terms of cost, for traditional manufacturing methods (especially injection moulding) processes. In fact, Steve Chillscyzn, the company's co-founder, CEO and president, says that leading with part cost, rather than design freedom, is the best way to find opportunities for 3D printing processes.
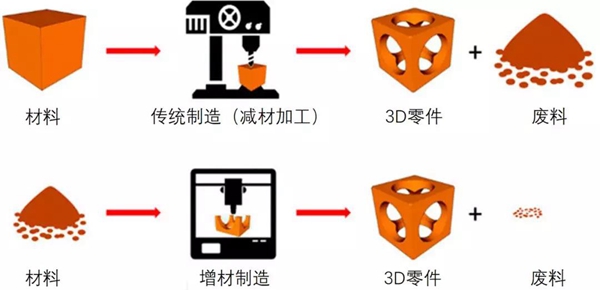
△3D printing has points for traditional processes, such as cost savings, faster manufacturing, reduced inventory pressure, solving the supply chain and improving design performance
To date, advances in 3D printing have been proving their commercial value by meeting needs that cannot be met by other production processes. Many of these relate to part consolidation, lightweighting, complex forms, customisation and small batch production. In most cases, the technology can justify the advantages of achieving improved performance by changing the original design, even if the unit cost is raised, which the customer feels is justified. But can there be a more balanced possibility in the future, where high speed mass production can be achieved and lower costs can be realized? So there are already innovations being made towards new methods that are more competitive with traditional processes, such as Evolve's development of a new 3D printing technology called STEP (Selective Thermoplastic Electrophotographic Process), which is capable of producing polymer parts at higher speeds and at a price closer to that of traditional processes.
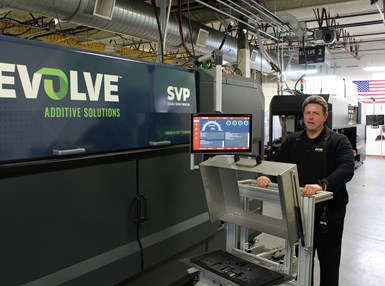
△Steve Chillscyzn is the CEO of Evolve. The company is looking for alternatives to traditional processes in terms of manufacturing speed and cost for 3D printing processes.
The company has spent several years researching these machines and production processes. The technology is broadly described as 3D printing that draws on high-speed 2D printing, but instead of printing documents, the process uses electro-photographic imaging to print layers of material. high-speed closed-loop control of X, Y and Z ensures precise resolution and consistency by rapidly building up parts and support materials and applying material combinations quickly within a single part. The company's Model SVP 3D printing system is capable of building at 286 cubic inches per hour, which means that one machine can deliver approximately eight tonnes of 3D printed plastic parts, per year, the CEO said.
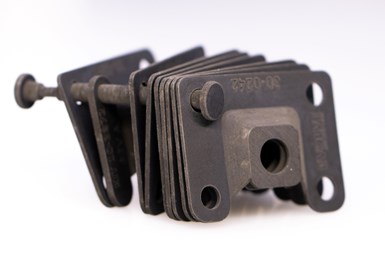
The company is offering test prototypes to selected customers, who can help the company evaluate the new machine and provide feedback on optimisation.
Chillscyzn said that part cost would be the fastest way to win acceptance for the STEP process. The advantages of 3D printing over injection moulding are attractive, including design advantages and freedom from machining. But the higher cost per part forces users to weigh up these advantages against the pros and cons. So the technology needs to overcome this hurdle in terms of cost. Fathom, a provider of digital manufacturing services, will be one of the customers receiving the next test prototype. evolve and Fathom will develop a STEP costing tool to more easily calculate and analyse response solutions.
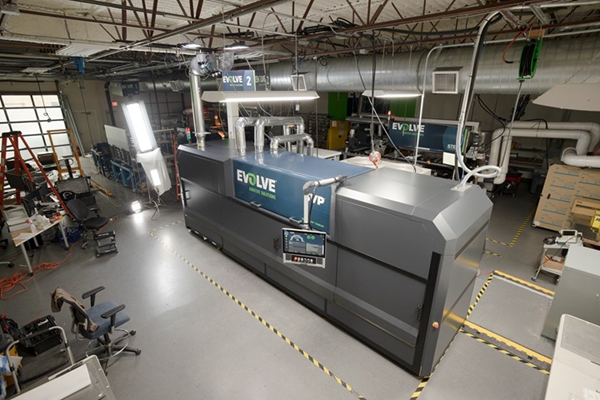
△This is a production part, but only 3D printing technology can now manufacture this type of bracket, including the connector ties. The technology therefore offers a particular advantage in terms of special builds
Lego and Stanley Black & Decker, are currently among the investors in Evolve. In the processing of special constructions, for example, a 3D printed fluid collection manifold with a built-in watertight ball valve and a set of nine associated brackets, these can be easily achieved using the technology, while at the same time reducing the pressure on stocks because of the possibility of on-demand manufacturing. But Chillscyzn says that in many cases, the new creative goals are a secondary priority for the technology. For now do matter, the technology must win acceptance as a production process on its own merits in order to change the wider use of the technology in parts processing.
In summary: 3D printing is fundamentally different from traditional manufacturing in that the simplified production method breaks through the limitations of traditional structural design and makes it possible to produce complex structures with optimised product performance. This increases manufacturers' production flexibility, shortens production cycles and brings truly innovative thinking to their products.
But, as Chillscyzn says, the first factor, for now, may be how to bring costs down and make the technology available to more traditional processes. But as the technology and materials advance, these will all be addressed in the future.