For orthopaedic implant manufacturers, finding a faster and easier way to generate and modify dot-matrix lattice design software with high design volumes to speed up design, build strategies for the 3D printing process and ensure the reliability of the 3D printing process is key to success. Join us today for an in-depth look at how Italian surgeons at implant manufacturer Lima are using Siemens NX AM to reduce design iterations, reduce errors and improve reliability.
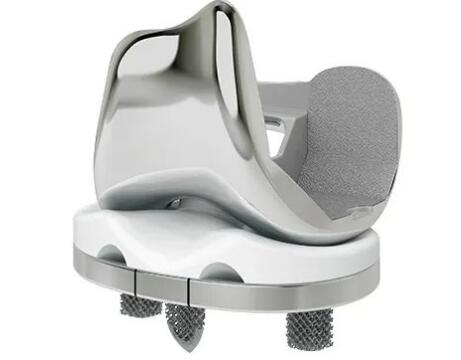
3D printed orthopaedic implants © Lima
3D printing - additive manufacturing allows local densities to be adjusted to loads and other requirements with the help of different material distributions. In addition, the weight, cost and production time of components can be optimised with the help of customised digital materials. Additive manufacturing (AM), a breakthrough production technology, becomes a process that allows efficient production of digital materials thanks to its geometrical freedom and mould-free production.
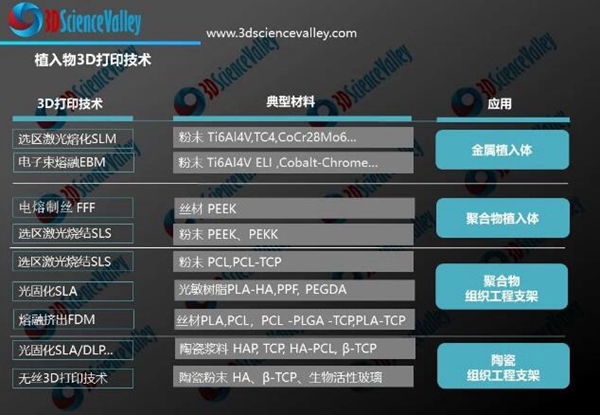
3D printed implants © 3D Science Valley White Paper
Better implants lead to better quality of life
Italian surgeons at implant manufacturer Lima, a global orthopaedic company, focus on digital innovation and customised orthopaedic implants to advance patient-centred care. Its product range includes joint implants, limb fixation solutions and specialised patient-specific prostheses. lima's most recent development has been the improvement of its 3D printing design and manufacturing process in collaboration with Siemens, resulting in a 50% reduction in AM-additive manufacturing modelling and work preparation time. lima's use of 3D printed "cementless The use of 3D printing for "cementless" implants has been around for a long time, according to 3D Science Valley's Market Watch it all started in 2005 when hardly any company was considering using 3D printing for mass production and Lima, a global orthopaedic developer based in Italy, was just starting to use 3D printing technology for rapid prototyping when it was not even possible to 3D print with the titanium material needed for implants. titanium material for 3D printing, and at the time had a high scrap rate of around half. Despite this, Lima was determined to pursue the industrialisation of 3D printing-additive manufacturing technology.
Today, from the initial purchase of EBM 3D printing equipment for the development of prototype acetabular cup implants, to the launch of the first full-fledged 3D printed acetabular cup implant, the Lima Delta TT Cup, in 2007, to today's TT technology for the manufacture of a wide range of orthopaedic products from hip to extremity, as well as customised implant solutions for specific patient needs. Lima's decade-long commitment has not only helped doctors solve numerous clinical challenges, but has also contributed to the advancement of 3D printing technology in the manufacture of orthopaedic implants. A major trend in the development of orthopaedic implants is the use of fractional lattice structures in joint replacements. These lightweight metal structures improve osseointegration - the connection between the implant surface and the living bone. Before the industry started developing metals based on fractional lattices - and even today - the gold standard for arthroplasty was to fix the joint with cement. In this case, inward bone growth was achieved by diffusion bonding with a plasma spray coating. This method results in low friction, low porosity and limited osseointegration. In contrast, the use of 3D printed metal implants with a punctate lattice structure, a non-cemented arthroplasty, brings the intuitive benefit that bone inward growth is enhanced over time.
Based on the objective function, the distribution of pore characteristics in AM additive manufactured porous structures can be homogeneous or inhomogeneous. Homogeneous scaffolds have cells of a specific shape and porosity, while non-homogeneous (gradient) scaffolds include arrays of cells in which the pore features vary spatially in the design space to achieve one or more functions in the scaffold.
Lima is not the only company to see the value offered by the use of dot-matrix lattice structures for implants. Its competitors have even acquired a company developing tantalum-based porous metals. The technology involves depositing tantalum on a polymer material and then using diffusion bonding techniques to bond it to a solid material. lima's vision was to combine porous and solid titanium in one step through 3D printing, without the need for a coating. To achieve this, Lima invented Trabecular Titanium™ (TT) in 2007. 3D Science Valley mentions Trabecular Titanium technology in the article "Ten years in the making, Italian orthopaedic medical device company Lima persists in building 3D printed implant products" as a technology that uses metal 3D printing equipment to manufacture titanium Unlike surface coatings made by processes such as plasma spraying, the 3D printed implants have a porous surface, which differs from a bionic structure made directly by the 3D printing machine, where the geometry of the pores can be precisely controlled. The porous implant structure created by metal 3D printing technology can facilitate bone ingrowth, leading to better rehabilitation outcomes.
Lima used Trabecular Titanium technology to manufacture the acetabular cups at a time when there was no international approval for 3D printed parts and convincing the authorities to accept the product Lima had made was fraught with challenges, with a full set of data having to be provided for validation, testing and quality assurance. Eventually, the regulator approved - which triggered an even greater challenge. demand was so high that Lima was immediately out of stock after it was certified. The state of metal additive manufacturing was unproven at the time, and the scrap rate for 3D printing was so high that Lima had to continue ordering more 3D printing-additive manufacturing machines to fulfil the order, and it took time to validate each one.
According to 3D Science Valley, it is currently possible to guarantee the safety of implants even for personalised custom 3D printed implants that have not had the opportunity to undergo multi-year clinical trials, through processes such as scientific and rigorous biomechanical evaluation and analysis during the implant design phase, rigorous monitoring of the 3D printing process and materials, and quality testing at a later stage.
Since the launch of the Trabecular Titanium cup in 2007, Lima has produced more than 100,000 cups with excellent clinical results and a 2015 study found that at least five years after surgery, the average Harris hip score improved from 44.2 to 95.9 out of 100. The cup has recently been awarded an Orthopaedic Data Evaluation Panel (ODEP) 10A rating, the highest rating for survival at 10-year follow-up. The success of the acetabular cup has convinced Lima to use Trabecular Titanium technology to 3D print other implants. But with more competitors in the market competing to utilise non-cemented arthroplasty, Lima needed to improve the speed and efficiency of its additive manufacturing workflow.
Key collaboration drives innovative knee replacements
When Lima decided to go for an uncemented total knee arthroplasty (TKA), the challenges would be more difficult than those faced by the acetabular cup. 3d Science Valley learned that hip replacement surgery is simpler than knee replacement surgery. The hip is a ball and socket joint, whereas the knee is a complex joint that allows for a wider range of motion. The knee implant consists of three components: the femoral component attaches to the lower thigh bone, the tibial plate attaches to the upper tibia and the polyethylene insert sits in between. The femoral component is a solid metal produced by precision machining.
To better understand how the walking motion transfers forces to the tibial plate, Lima worked with the biomechanics department at the Hospital for Special Surgery (HSS) in New York, where the team studied patients walking with knee implants to determine the optimal location and shape of the three contact points between the tibial plate and the bone.
The team also assessed the bone density of patients with implants in the USA and Italy. With these two studies, HSS Hospital performed a computer stress analysis of the contact point configuration to arrive at a design that included two porous TT nails, a porous anterior nail with a solid tip and a porous surface underneath the plate. This underwent several design iterations, including the number of pegs, location, shape, depth, etc.
This high level of iteration exposed areas for improvement in Lima's additive manufacturing process. 3D printing each change, a stl file had to be created and put into a different software package. Then, if there is another change, the subsequent conversion of the corresponding stl file is very difficult. The digital representation using the dot lattice structure further complicated the design and trying to edit the dot lattice structure from the STL file consumed a lot of computational resources, so Lima needed a faster and simpler way to generate and modify the dot lattice structure with a high design volume. In addition, the challenges Lima faced were not limited to the time delays associated with handling complex 3D printing files. For example, when manipulating STL files in an isolated software tool, the software tool introduces "digital discontinuities".
Lima needed a new approach to the design of its tibial plate and an integrated, linked digital thread through the design and manufacturing process. In this regard, Siemens NX and Teamcenter are part of the Xcelerator product portfolio, a comprehensive, integrated portfolio of software and services offered by Siemens Digital Industrial Software.
Addresses "digital discontinuity" in dot matrix lattice design
Lima evaluated NX AM in 2018 and shortly thereafter, Lima became a Siemens NX AM beta testing partner, making dot lattice design with lattice easier by reducing the reliance on STL files with NX AM and integrating seamlessly within Lima's Teamcenter environment.
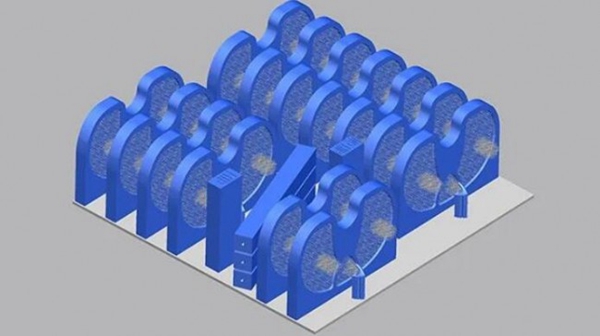
© Siemens
Using NX AM brings immediate benefits to the development of tibial plates. Designers no longer have to struggle with STL files and can parametrically edit most of the features of the tibial plate as they are mathematically related to the geometry. The use of NX AM also simplifies the task of designing Lima dot lattice structures. Taking into account all the characteristics of a proprietary lattice structure, custom-designed cells, with NX AM, Lima reduces the calculation time for designing trabecular titanium structures. And because it is almost completely parametric, design modifications are updated automatically. Whereas in Lima's old process, modifying STL files was disconnected from the workflow and therefore increased the risk of human error, understanding that everything in a single digital stream and one-click dot matrix design makes the whole process more efficient.
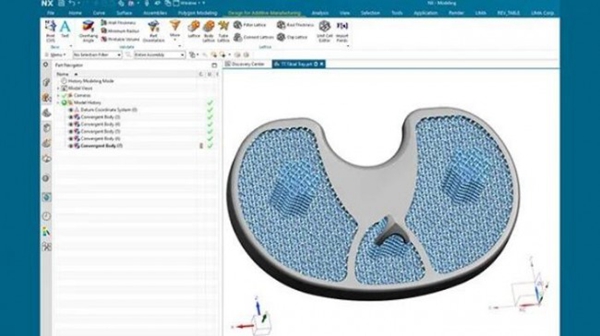
© Siemens
Lima is now not only developing a tibial plate, but is also producing it in 10 off-the-shelf sizes. This is quite significant for 3D printing towards mass production. lima currently has a range of sizes optimised for the global market, from small to large patients and people with different needs, each requiring adaptation of the characteristics of the tibial plate. 3D printing-additive manufacturing modelling and job preparation times have been reduced by 50% with NX AM. Through design optimisation, Lima can achieve better designs with less experimentation, reducing errors and increasing reliability through the Siemens software ecosystem. 3D printing has also helped manufacturers get one step closer to patients, and Lima currently has an additive manufacturing facility installed at HSS Hospital, where Lima's production engineers, using Siemens software, help surgeons develop patient-specific patient implants.