July 5, 2022 - France-based train manufacturer, Alstom, has now begun to adopt 3D technology and apply it to the company's industrial production system.
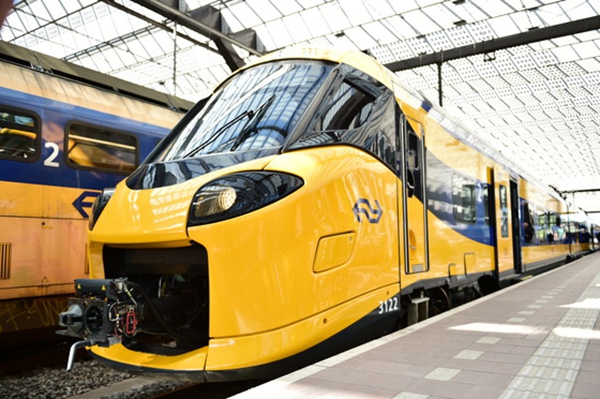
△Alstom France is a global leader in rail transportation, power equipment and power transmission infrastructure
By digitizing part of its own supply chain, Alstom has made achieving manufacturing flexibility, shorter lead times, and lower costs a key strategic direction for the future of the company. With the help of 3D printing provider Replique, Alstom is able to produce small quantities of metal parts for their trains in a modular fashion, enabling the company to better meet the local needs of its global customers. According to the latest developments in the partnership, the company has received and installed the first batch, of stainless steel door stop parts for trains manufactured by 3D printing. 3D printing, is now a key part of our supply chain," said Ben Boese, manager of Alstom's German Transportation 3D Printing Center. With Replique, we benefit from advanced 3D printing materials and related technical support, as well as decentralized manufacturing capabilities covering all relevant locations. Their end-to-end service allows us to respond to diverse customer needs faster and more cost effectively."
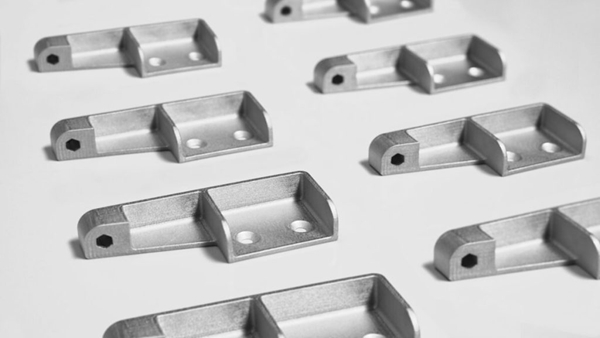
△ALSTOM's 3D printed stainless steel door stop
Trains are also gradually adopting 3D printing
In the train sector, the system contains a large number of individual moving parts. Specifically, ALSTOM is part of a multinational operation, so each train has its own set of part requirements. With traditional manufacturing, even small batches of parts inevitably, require tooling and other tools, which can lead to high upfront manufacturing costs and long lead times. 3D printing can help companies solve these challenges by enabling cost-effective on-demand manufacturing, regardless of batch size. While this may be the company's first use of 3D printing for volume production, the technology has actually been used by the company to address spare parts issues for a long time. "The 3D printing market is still very fragmented, which makes it impossible for end users to find the best solution for each part," Boese added. "But with Replique, we can benefit from a one-stop solution across all major 3D printing manufacturing technologies and materials.
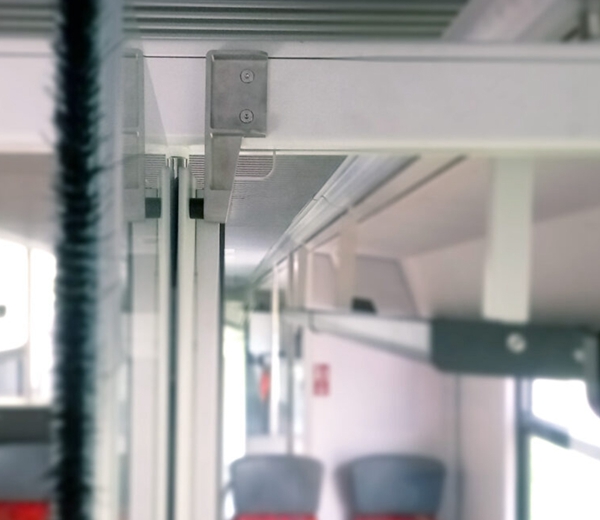
△ The door stop after installation
3D printed streamlined doorstop
Alstom needed multiple door stops to separate the first and second class compartments of the diesel train cars. The printed parts needed to be both durable and aesthetically pleasing because of their longevity, with strict design requirements. Ultimately they were FFF 3D printed using BASF Forward AM's Ultrafuse 316L stainless steel filament, as this proved to be more cost effective than metal powder bed fusion. after 3D printing, the door stops go through a degreasing and sintering process to achieve the final fully dense metal parts. replique delivered these door stops in just 1.5 months . During this time, they also underwent sufficient testing of pre-production samples to eventually receive approval for batch production. "We were able to produce the door stops at a much lower cost compared to traditional methods. In the near future, we plan to further exploit the potential of this technology by creating topology-optimized designs for new parts, and even making them lighter by reducing the filler," Boese concluded.