Satellite launched into "lunar orbit". Launched via an electronic rocket powered by the company's 3D printing engine, the microwave-sized "CAPSTONE" CubeSat is designed to pave the way for a human return to the Moon as part of NASA's Artemis mission. Specifically, the device will be the first spacecraft to enter a near linear halo orbit (NRHO), the planned orbit of the orbital outpost built to support lunar excursions.
"Today's launch is an important step in man's return to the Moon and a testament to the determination and innovation of the hundreds of people behind CAPSTONE," said Rocket Lab founder and CEO Peter Baker. "Rocket Lab was founded to open access to space and enable groundbreaking missions like this one that push the limits of small satellites. While Capstone's journey to the moon has only just begun, we are proud to be able to safely deliver Capstone to space."
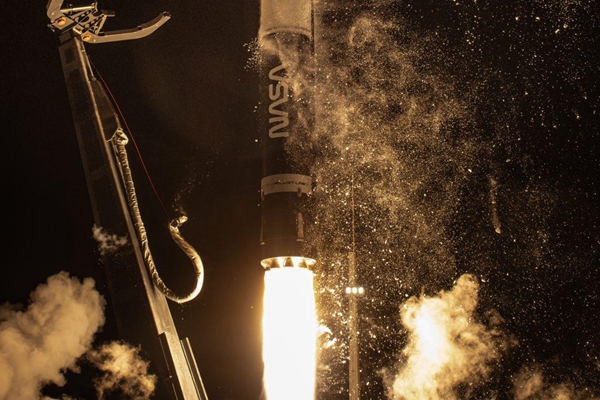
The E-Rocket takes off with the CAPSTONE satellite. Photo from Rocket Lab.
Rocket Lab's Rutherford engine
Having facilitated 147 satellite launches over the past 16 years, Rocket Lab has become a reliable partner for aerospace companies and space agencies, among others. To a large extent, the company's offerings revolve around its neutron and electron launch vehicles, which are powered by its electron beam melting (EBM) 3D printed Rutherford engines. Now 3D printed more than 100 times, the Rutherford is a liquid propellant-fueled carbon composite engine capable of carrying payloads of up to 225 kg and achieving 120N of thrust, making it ideal for putting small satellites into orbit.
Since Electron's first successful mission, Rocket Lab has been commissioned to launch several research and development satellites. In 2020, the company launched a weather satellite into space as part of the Air Force Research Laboratory's Monolith program. Earlier this year, the company was also selected to launch NASA's "VADR" payload, a $300 million program designed to help U.S. aerospace companies discover new opportunities.

The Photon Lunar spacecraft bus with the CAPSTONE satellite installed. Photo from Rocket Lab.
Paving the way for lunar return
NASA's Cislunar Autonomous Positioning System Technology Operations and Navigation Experiment or "CAPSTONE" satellite was built to facilitate its Artemis mission. For those unfamiliar, the main goal of the program is to return humans to the moon for the first time since 1972 and establish a base on the celestial surface. To accelerate mission readiness, NASA has often turned to additive manufacturing. Shortly after working with a team at Tuskegee University to test 3D-printed parts for the Artemis lander, the agency developed 3D-printed nozzles and combustion chambers that could be deployed in the program in 2020. With the June 28, 2022 CAPSTONE launch, NASA's latest adoption of 3D printing-enabled technology has now begun preparations for the deployment of Gateway, a space station designed to enable future lunar and Mars exploration.
CubeSat, manufactured by Tyvak Nano-Satellite Systems, will do this by experimenting with NRHO, an orbit that will see it pass nearly 3,000 kilometers from the lunar surface and as far as 70,000 kilometers, allowing it to be captured between the gravitational forces of the Earth and the Moon and rotate in sync with the latter, keeping it remain in place.
After announcing the "perfect" launch of CAPSTONE via Rocket Lab's Electron Launch Vehicle, NASA said it is now in a stable orbit, ready to be propelled to the Moon. Beginning with its initial orbit, the spacecraft bus on which CubeSat is mounted will perform a series of orbit-raising operations over a five-day period that will see its orbit extend into a prominent ellipse around Earth. Once this phase is complete, the device will launch toward the moon at 24,500 miles per hour, putting it into a ballistic lunar transfer that is expected to take four months. With the help of the sun's gravity, the CAPSTONE satellite is expected to be at a distance of 963,000 miles from Earth before being pulled toward the Earth-Moon system along a sinuous orbit that follows the gravitational contours of deep space.
Driving satellite development through 3D printing
Of course, 3D printing is not only used to build the rockets used to put satellites into orbit, it also continues to be used as a means of producing the equipment itself. Fleet Space launched a partially 3D printed Centauri 5 satellite earlier this month on the SpaceX Falcon 9 rocket, complete with a fully printed metal patch antenna.
3D Systems also recently announced that it has been contracted by Airbus to 3D print "key components" for the OneSat satellite. The device is designed to be fully reconfigurable in orbit, allowing it to dynamically change coverage area, capacity and frequency, built in part using the company's DMP Factory 500.
Elsewhere, companies such as Mitsubishi Electric have even come up with a way to 3D print satellite antennas in orbit in free-form. Using the company's technology, which is based around a newly developed liquid resin that can be photopolymerized by the sun's ultraviolet (UV) rays, it is possible to create parts larger than the satellite itself.